Bentleg opener seeding research an overview and update of the latest
Bentleg opener seeding research an overview and update of the latest
Author: James Barr and Jack Desbiolles (Agricultural Machinery Research and Design Centre (AMRDC), University of South Australia) | Date: 11 Aug 2016
Background
Tine seeders are recognised for their greater soil disturbance at seeding relative to disc seeders. Aspects of soil disturbance at seeding include furrow size and depth as well as the extent of soil movement or soil throw. The lateral soil throw, which is the sideways movement of soil pushed out of the furrow, is a particularly important parameter to consider in a no-till seeding context. A limited amount of lateral soil throw at seeding is typically desired to mechanically incorporate soil applied herbicides. However, excessive soil throw limits the furrow backfill and affects seed cover, and creates interactions (ridging) between adjacent seed rows, resulting in uncontrolled soil cover which can penalise seedling emergence and induce crop damage from pre-emergence herbicides.
In practice, these limitations hinder the adoption of narrow row spacing to increase crop competition with weeds, and reduce the machinery work rate at the critical time of seeding. An aspect overlooked in the soil disturbance issues at seeding is the role of furrow opener design features, and how they influence the extent and mechanics of soil movement. A novel bentleg opener concept originating in South Africa has been closely investigated at the University of South Australia over the last five years and GRDC/South Australian Grain Industry Trust (SAGIT) funded research is currently focussing on optimising the performance of bentleg openers for no-till seeding applications.
Figure 1: Bentleg furrow opener prototypes (left); Offset furrow effect of a bentleg design (right).
Bentleg openers - furrow loosening features
The bentleg opener design (Figure 1) offsets the shank portion of the opener away from the centre of the furrow where the upheaval of soil is greatest. The shank is connected to the soil loosening foot via a side leg portion. The foot has a low (45 degrees) rake angle, relative to most knife points, which improves opener penetration and reduces draft. A bevel edge is incorporated into the side leg and vertical shank to control splashing and contain the movement of soil towards the inside of the furrow.
These bentleg design features result in an opener that can loosen a large furrow size and achieve 100 per cent furrow backfill by virtually cancelling lateral soil throw at operating speed. Additionally, the soil loosening by lifting action is not disrupted by the shank and the loosened furrow soil falls back in place with minimal or no layer mixing. Figure 2 shows computer simulated furrow cross-sections contrasting the ‘bent leg + bevel effects’ which maintains soil layer integrity after loosening with that of a low rake angle, flat face, straight opener which lifts, mixes and throws soil layers. This feature of the bentleg opener was validated in soil-bin studies using tracers and is evidenced by the largely undisturbed and unburied furrow surface residue (Figure 5).
Figure 2: Loosened furrow profiles for a 35 degrees rake angle straight opener (left) and bentleg opener (right), obtained via DEM computer simulations.
Bentleg openers - soil throw evaluation in ‘dry-sowing’ conditions
A field trial was conducted in a dry silty-loam soil at Roseworthy (SA) in Sept 2014 to validate the potential suitability of bentleg openers for higher speed seeding. Using single tine runs, a 53 degrees rake angle straight opener was compared to two bentleg geometries with varying offsets (45 and 95mm) operating at three speeds (8, 12, and 16km/h) and set at a common 120mm operating depth. Draft, vertical and side forces, lateral soil throw, as well as furrow backfill were measured. Figure 3 shows snapshots of furrow profiles recorded using a laser scanning device and photographs of the large differences in soil throw during operation.
The 53 degrees straight opener showed the largest response to increased speed, significantly reduced furrow backfill and increased lateral soil throw between 8 and 16km/h. In contrast, both bentleg openers maintained 100 per cent backfill and operated with much less lateral soil throw. The data shows that the 45mm offset bentleg opener was sensitive to high speed, reaching similar soil throw to the straight opener at 16km/h, thus showing the need to optimise bentleg openers to suit the context of use. In this case (120mm operating depth), the 95mm offset bentleg opener was able to maintain a very low soil disturbance characteristics at speeds of up to 16 km/h. Figure 4 shows the drastic differences in the amount of soil tilth thrown out of the furrow (=’furrow spillover’) between straight and bentleg openers.
The bentleg openers were also able to minimise draft force and maximise penetration potential due to the relatively low rake angle of the leading foot (45 degrees).
Figure 3: Single opener soil movement trial at Roseworthy, SA (2014). Furrow profiles at 8 and 16km/h (left) and operation shots at 12km/h (right) for a straight 16mm, 53 degrees rake angle opener (top) and a 95mm bentleg opener (bottom).
Figure 4: 2014 Roseworthy single opener trial. Soil throw expressed as ‘furrow spillover’showing the great benefits of a suitable bentleg opener at speeds of up to 16 km/h (Error bars are ±1 standard error of the mean).
Comparing straight and bentleg opener layouts in moist Mallee soil conditions
A three row plot layout trial was conducted in a moist sandy-loam soil at Geranium, SA (2015) comparing straight and bentleg openers at 8, 12 and 16 km/h, and set at 100mm depth and 28cm row spacing. The two edge rows are used as a zero soil throw reference against the centre subjected to a two-sided soil throw (ridging) effect. Figure 5 shows no furrow ridging on the bentleg opener layout and no reduction in soil cover at the highest speed. In contrast, substantial ridging (+28mm) occurred with the straight opener, while the adjacent rows saw a greater emptying of the furrow (-7mm).
Bentleg openers thus represent a new opportunity for optimising the performance of tine seeders, enabling in particular high speed sowing operations, on the par with disc seeders, and without significant increase in soil throw. The work also demonstrated the need for dedicated research to optimise the bentleg opener design to suit the context of application.

Figure 5: Furrow profiles from a three row tine layout - straight (top left) and bentleg (bottom left) openers - operating in a moist sandy-loam soil at 100mm depth (Geranium, SA 2015). Note: the centre row simulates a seeder front rank opener subjected to a two-sided ridging effect from adjacent row opener soil throw. Pictures showing corresponding surface finish of 16km/h (right).
Bentleg seeding tine openers - residue handling
An interesting consequence of the controlled soil disturbance by bentleg openers was realised during field trials conducted in moist sandy-loam soil and heavy wheat residue conditions, using a six tine, four rank layout at 25cm row spacing. During the trial, minimal soil/residue interactions were highlighted (Figure 6) and by inspection of the resulting straw clumps being almost soil free and much lighter than under straight openers.
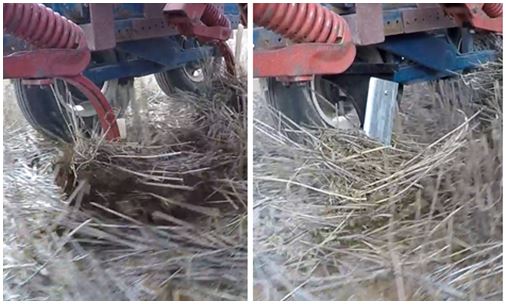
Figure 6: Key differences in soil/residue interactions between straight openers (left) and bentleg openers (right), leading to lighter and fluffier clumps with the latter.
One would anticipate that a given size clump created by a bentleg opener tine seeder, of lighter density, would have a much lesser impact on hindering seedling emergence, than a similar one of greater density created by a straight opener tine seeder. More work is required to verify such benefits. It is unclear if soil upheaved by a straight opener does in any way contribute to help clear residue off the shank, and promote smaller clumps, as no clear evidence of greater overall clumping could be observed under the bentleg opener layout.
Integrating bentleg openers into seeding systems: - seed / fertiliser placement options
Tine seeding systems vary in the way they achieve seed and fertiliser placement in the furrow. Banding systems can be split into:
- Delivery at tillage depth,
- delivery on a side-ledge above tillage depth, and;
- delivery into furrow backfill above tillage depth (with or without closer plate action).
Various single and double shoot versions exist, by combining or separating the above options for seed and fertiliser delivery, with or without furrow deep-tillage action, with or without adjustments relative to tillage depth, and delivering single, paired or ribbon seeding rows.
Currently, the use of bentleg openers on split seeding systems, where the seed banding device is regulated independently of the furrow opening tine, can be adopted once bentleg openers become available for a variety of tine shank designs. This has been informally investigated with Eyre Peninsula farmer Chad Glover (at Yeelana), using an adapter to suit the current bentleg opener design, with some success. The combination of bentleg tine followed by double seeding discs has successfully been used for high speed sowing in South Africa by Daniel Rossouw, the inventor of the larger size original bentleg opener RT Blade.
The option to retrofit single tine assemblies, as on chisel plough seeder bars, with bentleg seeding systems requires banding devices that are closely integrated with the bentleg opener. In this study, several seed and fertiliser banding device options were investigated to validate suitable double shoot bentleg seeding systems, as possible solutions to retrofitting tine seeder bars.
Control over fertiliser placement is important to ensure adequate separation from seeds and management of fertiliser toxicity. With double shoot systems, two approaches are typically taken to achieve either i) a well-defined ‘deep banding’ of fertiliser at a given depth, or ii) a ‘profiling’ of fertiliser over a depth range, reducing its concentration, but typically overlapping into the seed zone.
Seed and fertiliser placement accuracy was investigated in two sandy loam trials, namely Geranium, SA (2015 season) investigating banding boot options for the larger 95mm offset bentleg opener tested at a tillage depth of 120mm, and Loxton, SA (2016 season) investigating improved concepts for scaled-down bentleg designs (65mm offset), targeting a tillage depth of 90mm. Testing was conducted in moist conditions suitable for seeding.
Integrated fertiliser banding boot results
A fertiliser boot was constructed to follow the profile of the 95mm bentleg opener (Figure 7) with the outlet position of the chute set at 30mm below the soil surface. This banding boot was tested at the Geranium site in 2015. Fertiliser placement results for three speeds (5, 8, 14km/h) are shown in Figure 7. At a low speed (5km/h), fertiliser placement was shallowest in the furrow profile with a mean 70mm soil cover. As speed increased to 8km/h, the proportion of fertiliser at depth (beyond 100mm soil cover) greatly increased and the result was a ‘profiled’ fertiliser distribution, giving a relatively even spread of granules under a 30-130mm soil cover. At 14km/h, the fertiliser distribution became a ‘deep banded’ distribution, with the majority of granules being placed under a 97mm mean soil cover.
This speed related behaviour is typical of a delivery system relying on natural furrow closing to determine product placement depth. This specific banding device concept shown in Figure 7 would not be suitable for placing seeds, but would be satisfactory for separate banding of fertiliser in the furrow.
Figure 7: Geranium 2015 trial: 95mm bentleg fertiliser boot (left), fertiliser granule distribution with depth at three speeds (centre) and pictorial representation of fertiliser distribution changes under different speeds (right).
The above results represent one combination of bentleg opener and fertiliser boot design in one soil type. While the relative effect of speed on placement characteristics is likely to remain consistent, it is expected that in practice, relative changes in design features and soil conditions would alter the fertiliser distribution at any given speed. Additionally, the issues around boot outlet blockage risks have not been evaluated.
Integrated seed banding boot results - concept I (standard bentleg)
Two methods of seed placement were evaluated over two years using large size (95mm offset) bentleg openers (operating at 120mm) at the Geranium 2015 site, and scaled-down (65mm offset) bentleg openers (operating at 90mm) at the Loxton 2016 site.
Figure 8: Bentleg seed banding boot concept I. Seed placement results for two design iterations using a trailing closer plate principle at the Geranium 2015 site (left), and at the Loxton 2016 site (right). Error bars represent average standard deviation of sample (n=4).
The first method of seed placement aimed to place seeds by positively interacting with the furrow backfill using a closer plate principle (Figure 8). Results for the first design iteration (used at Geranium in 2015) are illustrated in Figure 8 (left), and show this concept worked well at five and eight km/h, achieving a mean seeding depth close to the target of 40mm and with low vertical spread. However, as speed increased to 11km/h, an increasing proportion of seeds reached greater depth due to unreliable closer plate interaction with backfill, resulting in deeper placement (80mm) and a trippling of the vertical spread. This issue stabilised at 14km/h where the mean depth reached 85mm with a reduced vertical spread, indicating the greatest proportion of seeds at depth occurred at the highest speed. This speed dependent performance is explained by the soil flow over the side leg creating a greater gap behind the opener as the speed increases and cancelling interaction with the fixed closer plate device. This issue implies that this particular concept is little suited in practice for seed placement.
In the second year, to try and reduce this interaction with speed, a modified approach was implemented consisting of:
- Reducing soil upheave through a scaled down bentleg design operating shallower (90mm) and using a thinner sideleg (from 16 mm to 12mm), and;
- increasing the closer plate thickness to ensure a more reliable interaction with the loosened soil. Another method to improve the closer plate action is to locate it further behind the opener. However, this increases the bulkiness of the assembly and its sensitivity to tine breakout.
This modified concept was evaluated at the 2016 Loxton site and resulted in a seeding system that placed seeds consistently at 50mm depth over the 8-12km/h speed range and with a comparatively reduced vertical spread (Figure 8, right).
Integrated seed banding boot results - concept II (winged bentleg)
A second method of seed placement was evaluated, which placed seeds on an undisturbed ledge in the side of the furrow through the use of a side wing added to the bentleg opener.
Figure 9: Bentleg seed banding boot concept II. Seed placement results for two design iterations suited to a ‘winged-bentleg’ concept at the 2015 Geranium site (left), and at the 2016 Loxton site (right). Error bars represent ±1 average standard deviation of sample (n=4).
This approach is similar to that used in many side-banding and paired row seeding systems and has a distinct advantage of not relying on soil backfill, therefore expecting to control the effect of speed on seed placement. This winged-bentleg concept was evaluated at both the 2015 Geranium and 2016 Loxton sites.
This benefit was confirmed with both design iterations (Figure 9), observing no significant change in mean seeding depth and relatively small vertical spread values. However, the increased soil disturbance (e.g. soil throw) resulting from the added wing component significantly reduced soil cover at greater speed while also increasing soil cover of adjacent seed rows via ridging. The difference in soil cover between adjacent seed row locations at the highest speed reached an average +23mm with the larger 95mm bentleg opener (operating at 120mm) at the 2015 Geranium site, while being reduced to only +6mm with the scaled-down bentleg version (operating at 90mm) at the 2016 Loxton site. This difference is attributed to the deeper positioning of a thinner and more streamlined wing design into the furrow.
Performance of bentleg seeding systems - wheat establishment
At the 2016 Loxton site this season, a number of integrated seeding system options with the scaled-down bentleg openers were compared at 8 and 12km/h with a common knife point system. All bentleg seeding systems were able to establish a similar wheat crop and displayed no emergence penalty at the 12km/h speed (Figure 10). A small emergence loss associated with ridging of 10plants/m2 (-8%) was observed with the winged bentleg opener. In contrast, the control knife point seeding system which registered a significant furrow ridging effect of +29 mm as a result of excessive soil throw at 12km/h, showed a significant reduction in plant density of 30plants/m2 (-23%).
Complementary work at Loxton is also suggesting no negative impacts of pre-emergence herbicides on crop safety with the bentleg seeding systems (detailed results to come).
Figure 10: Grenade CL Plus wheat emergence results in mallee context for two bentleg seeding systems at two speeds relative to a common knife point control (Results shown for two types of seed row: + and – soil throw). All openers had a common operating depth set at 90mm. No pre-emergence herbicides used.
Conclusions
Straight openers (e.g. knife points) cause excessive soil disturbance at seeding which often results in emergence losses due to furrow ridging and chemical damage from pre-emergent herbicides. In this context, bentleg openers offer an unprecedented opportunity to control soil disturbance characteristics, and minimise the impact of speed on lateral soil throw and furrow backfill. Research work to date is suggesting that bentleg openers could successfully be integrated into seeding systems that can increase operating speeds by 50 per cent with no penalty to wheat crop emergence, in contrast with common knife point seeders used in the industry.
Future work will need to broaden the performance validation of bentleg seeding systems over a range of crop types and soil conditions. Discussions with potential industry partners expressing a commercialisation interest are on-going.
Acknowledgements
This research is a collaborative project between the GRDC, SAGIT and University of SA. The research undertaken as part of this project is made possible by the significant contributions of growers through both trial cooperation and the support of the GRDC, the author would like to thank them for their continued support.
Contact details
James BarrUniversity of South Australia, AMRDC Office J2-08, Mawson Lakes Campus, Mawson Lakes, SA 5095
0417 823 623
james.barr@unisa.edu.au
@JamesBarr_
Jack Desbiolles
University of South Australia, AMRDC Office J2-08, Mawson Lakes Campus, Mawson Lakes, SA 5095
08 8302 3946 ; 0419 752 295
jack.desbiolles@unisa.edu.au
Was this page helpful?
YOUR FEEDBACK