Spray application manual
7 June 2025
Published 24 January 2025 | Last updated 20 January 2025
The ideal batching system would allow for a total tank mix volume equivalent to the main sprayer tank to be mixed, agitated and ready for transfer as the sprayer pulls up. To implement this strategy successfully usually requires two people: one to complete the mixing and batching while the other sprays the load.
Where it is not possible to batch an entire load, consider using vats to simplify the mixing process and to speed up dispersion and transfer of products to the sprayer.
Find out more
For more information and case studies on batch mixing set-ups, refer to the GRDC publication Mixing and Batching For Agricultural Chemical Application.
Considerations for mixing vats
The mixing vat should be of a suitable size to hold and dissolve enough of the product to match the size of the spray tank. This is why it is important to check the product’s safety data sheet (SDS) for the solubility of dry products, then compare how much product is required for a full spray tank, and what volume the vat will need to hold to fully dissolve that much product.
For liquid products it is useful to have accurate measurements in the vat to reduce the time required to measure the product, for example, when transferring product directly from a shuttle into the vat.
Measurements in a mixing vat
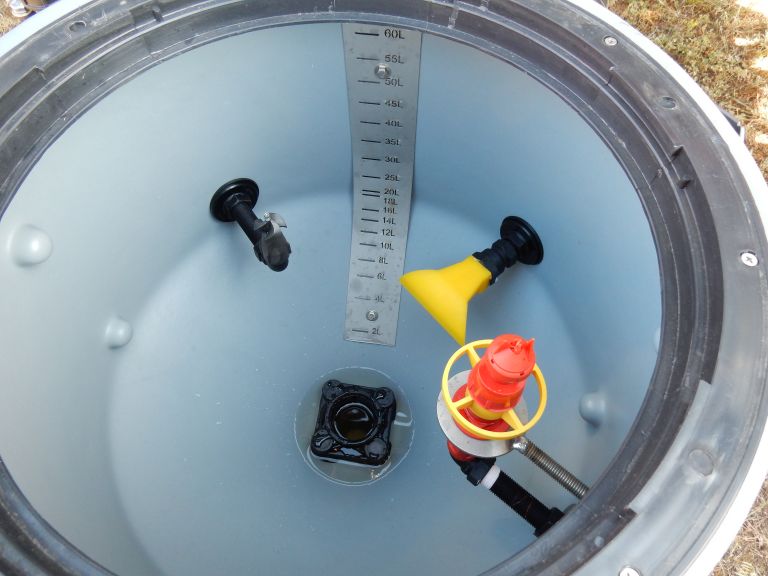
Useful mixing vat features:
made of a durable, UV-stable material that has a smooth internal surface to allow for better decontamination;
a cone-shaped base with a flat sump, so a tank outlet and anti-vortex fitting can be easily installed into the base, such as a Banjo Bottom DrainTM manifold bolted tank fitting;
a lid that is large enough to allow drums to be rinsed easily;
fitted with a drum rinse nozzle;
no internal ledges that may trap solid products;
the system should have the ability to isolate the mixing vat from other plumbing;
the ability to suck out of the side of the mixing vat, and a return to the bottom of the mixing vat;
a way of preventing debris from entering the spray system, such as a perforated base plate inside the mixing vat; and
modified handles, such as extensions, or foot pedals to allow for ease of operation.
Perforated stainless steel mesh in the bottom of a mixing vat
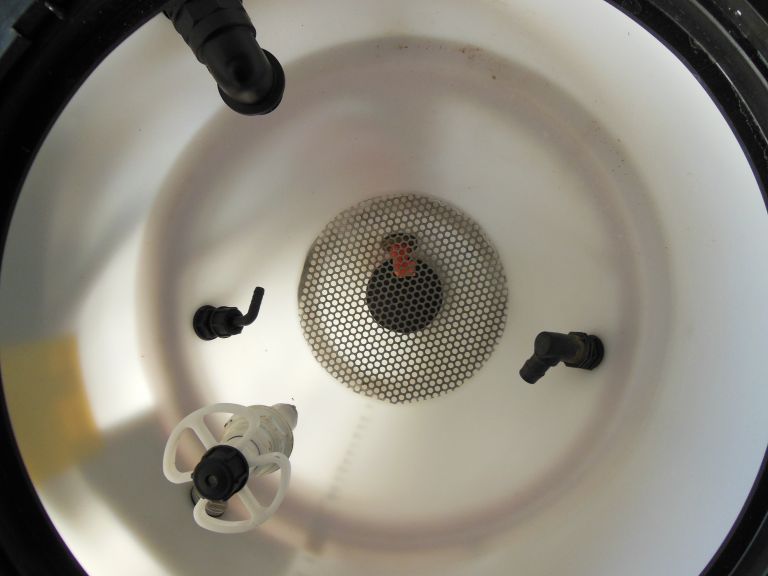
An anti-vortex fitting added to the outlet of the mixing vat
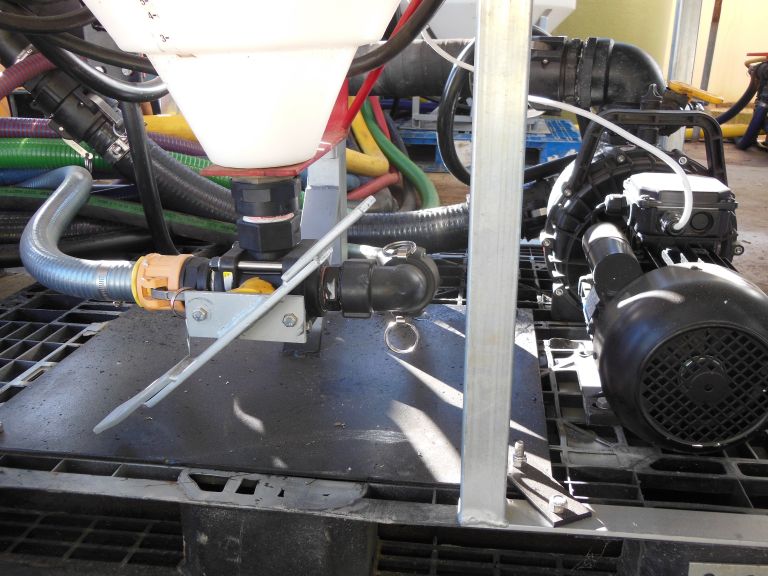
An extended tap handled fitted to the tap of the mixing vat to improve operator access and safety
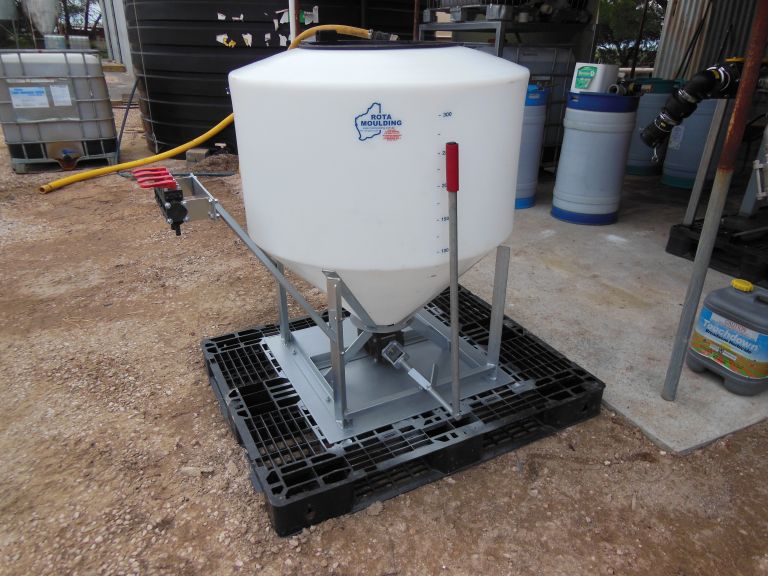
Tips
Solid products and suspension concentrates (flowables) will dissolve and disperse more easily if the vat is as full with water as practical before introducing these products. When adding these products into the vat, add them as though you are pouring liquid out of a 20L drum – slowly. Another good option is to pump water into the bottom of the vat as this will dissolve the products more easily.
Install and use a tank rinse nozzle in the mixing vat to enable flushing of the vat and potentially settle any foam.
Use an anti-vortex fitting on the tank outlet to reduce the possibility of sucking air.
Use an outlet that enables the mixing vat to be totally drained without any residue being left in the mixing vat e.g. Banjo Bottom Drain™, manifold bolted tank fitting.