Spray application manual
4 June 2025
Published 24 January 2025 | Last updated 20 January 2025
Where diaphragm pumps are fitted, always check the oil level and condition, and that the bearings are greased (where required) before operating the pump.
For new sprayers fully flush the spray system with water to remove possible debris from the tank, filters, lines and nozzle bodies.
Even with new sprayers it will be important to fully flush the spray system to ensure they are clean and free of metal and plastic fragments from drilling, grinding and cutting operations that may have occurred at the factory or at the machinery dealer.
For used sprayers fully decontaminate the machine before conducting any checks of the sprayer output.
When you are not sure what the sprayer has been used for in the past, or how clean it may be, treat it as if it has had a Group 2 herbicides in the tank. Decontaminate using chlorine-based products, followed by an alkaline detergent or tank and equipment cleaner. The cleaning process must be thorough.
Check all filters and screens, spray lines, boom sections and end caps or taps, nozzle bodies and non-drip diaphragms for debris or residue and clean as required.
For more detail on decontamination procedures and cleaning agents go to Module 7: Mixing and decontamination.
Always check for residues in blindspots
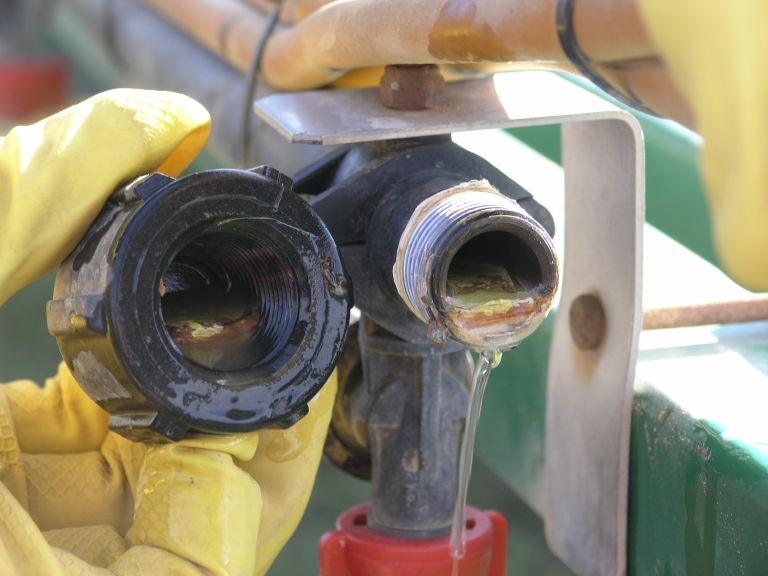
When reassembling components that have seals, use rubber grease to lubricate all of the gaskets and o-rings.
For all sprayers, check and service all of the nozzle bodies
If there are multiple outlet nozzle bodies on the sprayer and they are not easy to rotate they should be serviced.
Remove the nozzle cap, nozzle, nozzle gasket, non-drip check valve, diaphragm and turret.
Put all parts in a bucket of hot, soapy water. Clean parts with a toothbrush. Turn the check valve upside down, put under water and push the plunger many times to flush any dust, grit etc. from under the spring.
Compare non-drip check valve diaphragms with a new diaphragm: if they appear buckled or distorted, replace them.
Use rubber grease or similar on all rubber components when putting the nozzle body back together again.
Initial test drive (operate with water in the tank)
The initial test drive should be used to check what a suitable spraying speed will be and that these speeds align with the spray plan. This test should also be used to check that all of the systems fitted to the sprayer are functioning correctly.
Make sure you fill the tank to evaluate how the sprayer and systems perform with the tank at different levels.
Before you start the test drive, check diaphragm pumps again for oil level and condition.
While driving the machine, check:
that the desired rate (litres per hectare) can be achieved;
that systems are communicating correctly – e.g. GPS and rate controller are ‘talking’ to each other (where separate);
auto-steer responses at different speeds
that the auto section control is turning on and off as required;
boom stability and the auto-height control (where fitted) responds correctly; and
that the desired application rate (L/ha) is stable at a range of speeds.
Tip
If litres per hectare (L/ha) fluctuates while you are spraying, put the rate controller into ‘manual’, operate the sprayer at your constant spray speed and check that the L/minute and kilometre per hour reading are steady. If they still not steady in ‘manual’ check what is causing them to fluctuate. If they are steady in ‘manual’, lowering the regulating valve setting may improve this when operating the rate controller in ‘auto’.
Find out more
For more information about preparing a Spray Plan, go to Module 5: Spray Plans
At the end of the test drive.
For sprayers fitted with diaphragm pumps, replace the pump oil and check bearing grease (where required).
Do a complete calibration
Once the sprayer is clean, the spraying speed has been established and you are confident the major systems are operating correctly, it is time to ensure the accuracy of the output of the sprayer.
Never assume that the sprayer has been correctly calibrated, even if it is new.
Before undertaking the calibration it is a good idea to know what products are likely to be used and how these will need to be applied. Preparing spray plans will help to identify the types of nozzles to be used, along with appropriate settings for the controller, as well as the figures to check during calibration and spraying.
Many new sprayers are supplied without the nozzles fitted. Generally the operator must nominate what nozzles they requires. This can be difficult to determine if you have not established a range of suitable spraying speeds for your situation.
It is important to establish the spraying speed before you select nozzles and calibrate the sprayer output.
Operators should allow enough time between delivery and operation to ensure they can choose the right nozzles, based on their actual spraying speeds.
A complete calibration means checking:
the flow meter and calibration;
the speed sensor and speed calibration;
the main spray tank volume and graduations;
pressure at the nozzle and gauge accuracy;
controller settings against a spray plan; and
nozzle outputs (check every nozzle).
Where calibration factors need to be adjusted, record any changes made and the date they were made in the controller manual or a logbook that remains with the sprayer at all times.
Tips
For second-hand sprayers, pull the flow meter apart and wash all the components to remove any foreign material, e.g. iron, surfactants, chemical etc.
Put the flow meter back together, checking that the impeller is spinning freely and that there is a slight noise when you shake the flow meter.
This will be the impeller float moving from end to end.
A flow meter impeller jammed by residue

Stationary tests using the rate-controller functions and system performance
Use the 'simulated speed' or 'test speed' function in the controller to check that the sprayer is working properly.
Program the maximum spraying speed identified on the spray plan, switch the controller to 'manual' and decrease the pressure until there is no pressure in the system, then increase the pressure until the pressure stops going up. Note these and check against the pump capacity as it may indicate possible restrictions on the delivery side of the spraying system or poor pump performance.
Put the controller in 'auto' and check that the sprayer can achieve the required L/ha at the intended spraying speed.
Program the average/constant speed on the spray plan into the controller, put the rate controller into 'auto' and check that all the figures on the rate controller screen (L/min, pressure at the nozzle, L/ha) match the figures on the spray plan (what you calculated them to be).
Pre-operational checks
15 January 2025Spray system pre operational checks. Another video from GRDC's Spray Application GROWNOTES™ series.
Tips
If the sprayer is unable to achieve the required litres per hectare,
have the sprayer operating with the nozzles turned on and check inside the spray tank. Look for an abnormal amount of flow going back in to the tank. Follow the hose back to the component that is allowing the flow to go back into the tank.
Using the speed simulation function for stationary tests
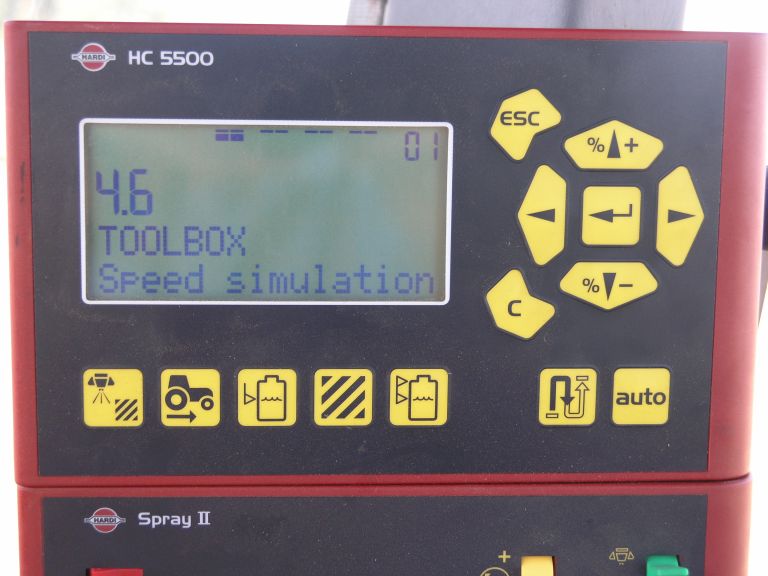
A John Deere nozzle flow-check screen
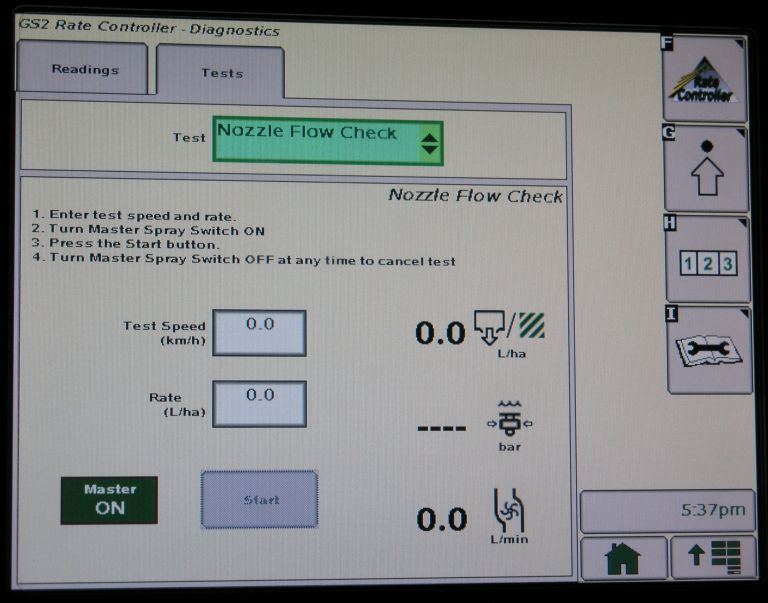
Turn each boom section off individually to see if the allocated switch is turning off the correct boom section, to make sure that the L/ha and pressure are correct, that the total flow (L/min) has changed and that the system is regulated quickly. Do this for each boom section and adjust the regulating valve setting if the L/ha does not go back to the programmed L/ha quickly.
Enter a speed below the minimum speed on the spray plan, put the controller in ‘auto’ and check that nozzle pressure does not drop below the programmed setting.
When the sprayer is operating at a simulated speed below the minimum speed it is also a very good time to do a ‘physical check’ of all the nozzle spray patterns and to make sure all the nozzles bodies are working properly.
Check the accuracy of the pressure gauges fitted to the machine.
Double-check all the settings in the rate controller, especially the minimum setting (e.g. pressure, speed or total L/min), ensuring that it will hold a minimum pressure to achieve the required spray pattern.