Spray application manual
7 June 2025
Published 24 January 2025 | Last updated 20 January 2025
Set aside several days each year that fit in with your cropping program and other commitments to fully check over and maintain the sprayer.
Always conduct a thorough decontamination of the sprayer and all mixing and transfer equipment at least once a year, even if you have dedicated spray equipment that does not need in season decontamination as it is not being used for different types of products or spraying different crops.
This is the opportunity to really give the equipment a good soak by leaving cleaning agents in the spray, mixing and transfer systems overnight, followed by a thorough cleaning and rinsing process. Give everything a complete wash down, inside and out, to remove potentially built-up residues.
Always complete a full calibration of the sprayer and other metering devices at least once per year.
Making sure you check the accuracy of all equipment, including:
the flow meter and calibration factors;
the speed sensors and speed calibration factors;
infill meters and chemical transfer meters;
tank volume, (if the tank has changed shape or been damaged);
pressure at the nozzle and accuracy of pressure gauges;
controller settings against spray plans; and
nozzle outputs for all sets of nozzles.
Always check all devices that provide inputs to the controller (speed, flow, pressure) and the serviceability of measurement devices used for mixing and transfer operations.
Checking pressure at the nozzle to compare against other gauges and the controller
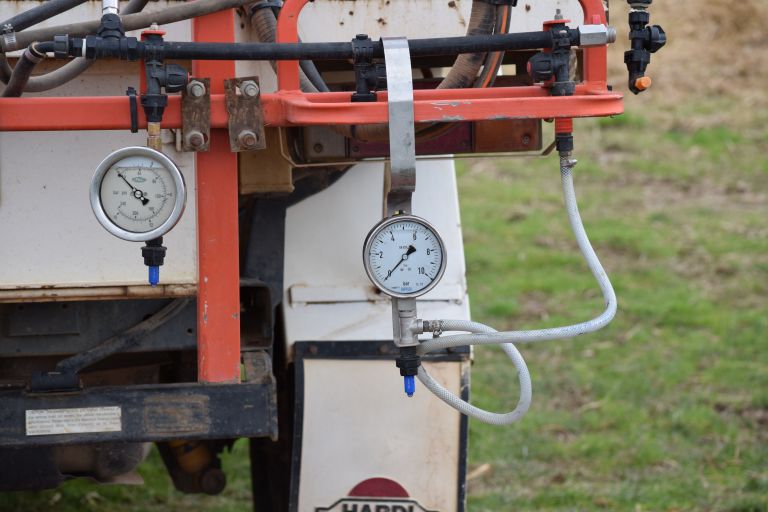
Options for measuring pressure at the nozzle
24 January 2025Options for measuring pressure at the spray nozzle. Another video from GRDC's Spray Application GROWNOTES™ series.
This video appears in modules 6 and 8. Craig Day: Okay, if we're going to look at doing pressure and flow right at the nozzle, I just want to walk you through a couple of gauge options here. These are the gauges that I use when I'm doing testing for calibration and sprayer check-out. A very simple gauge for us to make up at home incorporates a T-Jet threaded cap, a T-Jet nozzle fitting at the bottom, some gas fittings, a T-piece and preferably a rear-entry gauge. The rear-entry gauge will enable the gauge to sit vertically when doing the testing. Pressure is critical. When you're buying a gauge, if you're operating your spray system at three bar, aim for your testing gauge to have three bar at about twelve o'clock on the gauge. That'll mean the gauge will work within a very comfortable range there. If we put an inaccurate gauge on your sprayer and you go and rely on that for a test, we need to actually check the gauge we've bought. So, if you go back to your nozzle chart and look at the flow rate of the nozzle at three bar, in the case here we have an 03 nozzle that will be doing 1.2 litres per minute at three bar. So if we set this up, your new testing gauge, put it on the sprayer, set this gauge to 3 bar and actually weigh the water, we'll know how accurate your gauge is. |
Run through many of the checks that were done when the machine was first delivered, including checking:
filters, o-rings, nozzle bodies, diaphragms and seals are in good condition;
pump capacity and for signs of wear or fatigue;
plumbing – condition of hoses and fittings, clamps etc;
electrical connections for corrosion, etc.;
fatigue and wear points;
boom stability and height control; and
tyre wear and condition.
Also make sure you check the following during the annual check:
mixing and transfer equipment is in good condition and appropriate for future jobs;
PPE requirements (including cab filters) and their serviceability for jobs that are likely to be done next season; and
decontamination agents and procedures that might be needed for future jobs.
Find out more
For more information on decontamination or calibration go to Module 7: Mixing and decontamination and Module 8: Calibration of the spray system