Spray application manual
7 June 2025
Module 1: Planning for spray application
1.2: Identify ways of increasing your capacity and efficiency
Published 24 January 2025 | Last updated 20 January 2025
Although the time spent spraying is usually only a fraction (often less than 50 per cent) of the total engine hours on the machine, this is not always considered by operators.
There are many things that can be done to change this ratio and to increase your ability to cover the country in a timely manner before buying a bigger, wider or faster sprayer.
The most obvious place to start is to reduce the time spent out of the paddock. Some considerations include improved facilities for filling; mobile mixing plants to take water and pesticides to the field rather than needing to drive back to the shed and front filling points on the spray rig so that booms do not need to be folded before refilling.
Things that can speed up mixing, transfer and filling the water tanker/water cart
The ability to transport enough water for a full day’s spraying close to the sprayed paddocks can save a lot of time and reduce engine hours on the sprayer.
Mixing trailer (portable set-up)
A mixing trailer that allows you to transport chemical to the site and has all the equipment required to safely mix your chemical and transfer it efficiently to the sprayer will also save time. Whatever system you use, there are many off-the-shelf products to make it easier to set up.
Chemical mixing vat
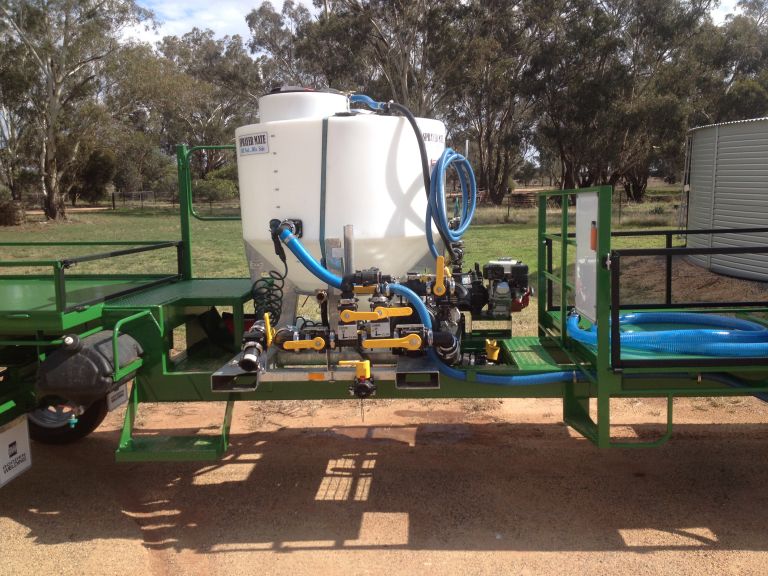
Chemical vats
Chemical vats can speed up mixing, particularly of powders. The vats can help dissolve products before they go into the tank and can get product into the sprayer more quickly. To reduce the risk of compatibility issues, it is important to fully dissolve/suspend each product before the next is added. Mixing vats with high agitation are good for this task and then can be quickly pumped into the main tank before the next product is added to the mixing vat. Be particularly careful if attempting to add multiple products to the mixing vat. Water volume is limited and mixtures will be concentrated, increasing the risk of product incompatibility occurring.
Chemical trailer
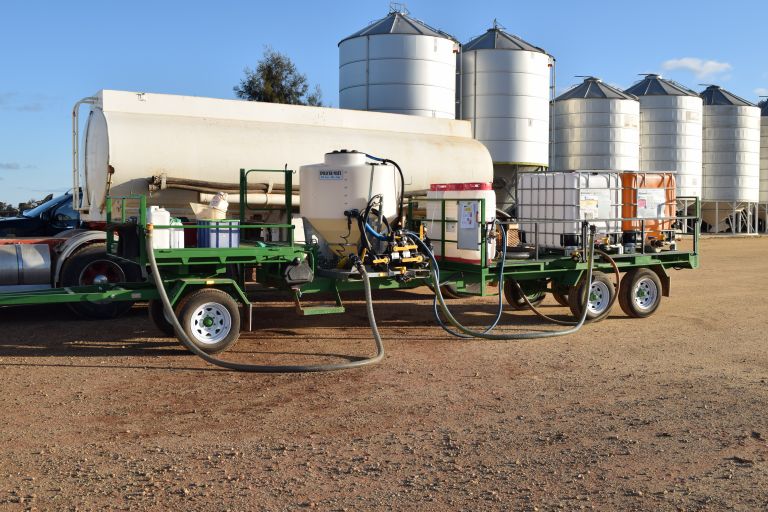
Closed mixing systems and chemical transfer pumps
Chemical transfer pumps can increase the accuracy of measurements. Using closed mixing systems, such as Envirodrum® or shuttles, can reduce the risk of operator exposure to chemicals.
Find out more
For more information, go to Module 9: Mixing and transfer systems.
Chemical fill points
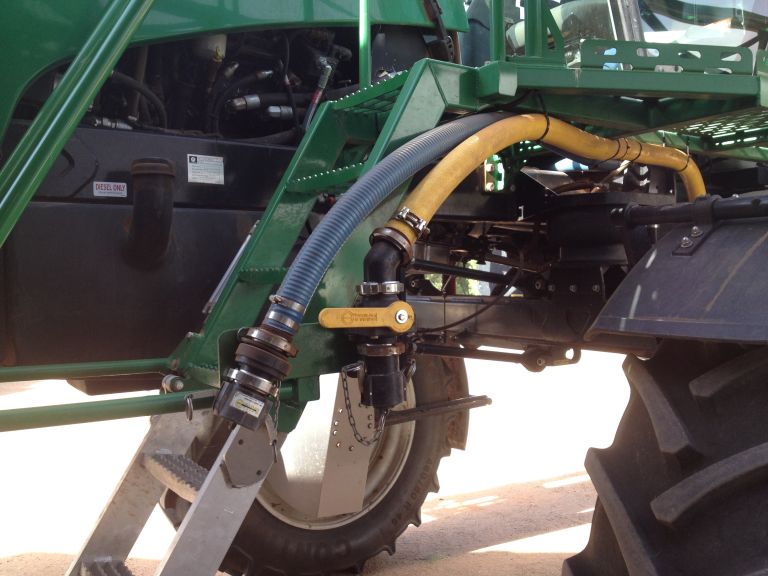
Easier access to fill points on the sprayer (using an external pump)
Front fill points make it easier to drive to the mixing area, and are easier to access to improve fill times. Using an external pump to fill the sprayer will also help to reduce engine hours.
Mixing and handling - Custom trailer
18 December 2024Mixing & handling spray chemicals and the benefits of a custom made trailer. Another video from GRDC's Spray Application GROWNOTES™ series.
This video appears in modules 1 and 9.
David Gooden: So we've designed this chemical mixing trailer to contain all the chemical that we need. We've purchased a mixing unit because we thought it had all the features that we needed to mix our chemical correctly. Some of the features with the mixing unit is that it has a cone tank and doesn't have any ledges inside which can retain chemical residue. It holds enough water for a full batch. It also uses the pump to suck the chemical and therefore not creating any air and foaming like a venturi system would. We run a clean water pump to keep the chemical and the clean water system separate. We run dry mate fittings in order to reduce the risk of chemical spill and we also use micromatic fittings to
suck from enviro drums.
The trailer has been designed to hold enough chemical for a whole day spraying,
we've got room for dry product, enviro drums and IBCs. We bring the clean water to the paddock in order to make it more efficient and on top of that we've brought the filling point of the sprayer to the front in order to make it quicker in the paddock to fill up.
Making use of weather-forecasting tools
Where possible, make use of weather-forecasting tools to help define your spraying windows over the coming week; knowing which days, and hours within the day, are likely to be suitable for spraying and which are not can help you to plan your week.
Several websites make weather forecasts of up to seven days available. Some of these websites are specifically designed for spray operators and indicate factors such as Delta T (a measure of evaporation potential), rainfall, frost and inversion risk.
www.bom.gov.au/australia/radar
https://www.syngenta.com.au/weather
https://www.goannaag.com.au/wand-network
https://cotl.com.au/about.html
Improve maintenance to reduce downtime
Service availability is critical to sprayer ownership. Choosing the right dealer is just as important as selecting the type of sprayer you will use. Before purchase make sure you are confident the dealer can provide the services you will require:
regular inspection of the sprayer – regular checks can prevent bigger problems later on;
a plan for maintenance out of and during the season;
keeping commonly needed spare parts on hand – whether it is a filter, o-rings, spare nozzles or nozzle bodies, a replacement flow meter or even a main pump, it can be useful to have replacements available to minimise downtime; and
keeping things clean and calibrated – including nozzles, flow meter and components. Even new sprayers should have their nozzles removed and the tank flushed before the first use. Calibrating and checking major components (tank levels, flow meters and controller settings) should also be done before the first use and should continue throughout the sprayer’s life. Always flush the sprayer after use and do a full decontamination before changing product type or situation.
If you have done as much as you practically can to reduce the time spent out of the paddock the next step is to look at improving the efficiency of your spraying operations in the paddock.