Spray application manual
7 June 2025
Published 24 January 2025 | Last updated 20 January 2025
Flow meter calibration should be carried out at least once every 12 months, preferably more often, or when a replacement flow meter is installed.
Calibration of the flow meter is also recommended when increasing the litres per minute delivered by the spray unit as a result of fitting significantly larger nozzles, for example, going from 02 to 04 orifice sizes.
Flow meter PPU figure on cable
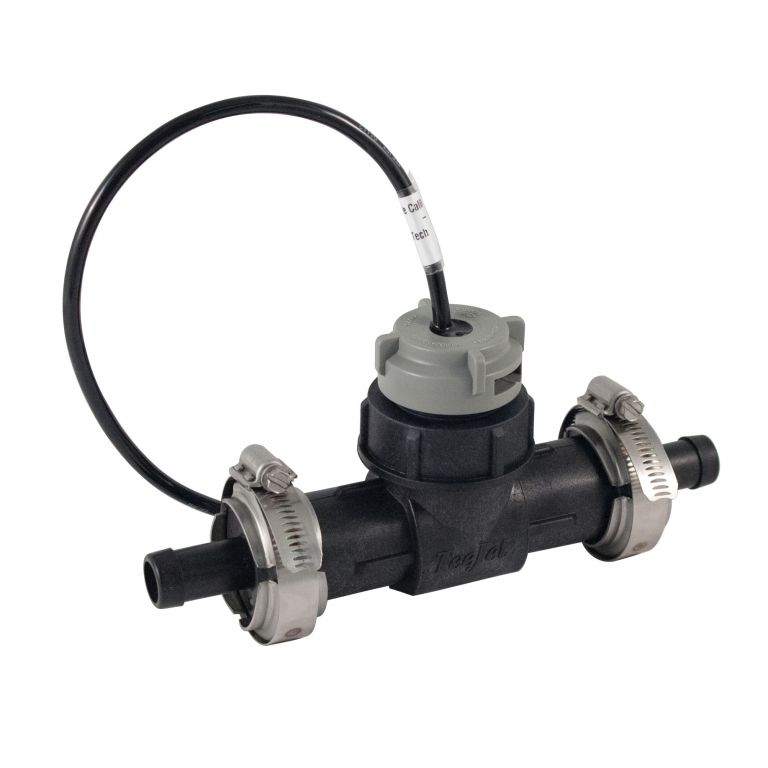
All flow meters come with a factory calibration number tag figure. For example, a tag figure of 120 pulses per unit (PPU) indicates the number of pulses that come from the flow meter to the rate controller while one litre of water passes through it. The adjustment of this flow constant can be achieved by fine-tuning this figure using the following steps.
NB: before commencing, it is assumed that you have already measured the pressure at the nozzle.
Step 1: Record the flow meter constant.
Step 2: Operate the entire boom at the desired working pressure. Record the total litres per minute for the entire boom from the rate controller.
Step 3: Compare the rate controller readout to the actual litres per minute already calculated from weighing the nozzle outputs.
If there are concerns about the accuracy of the flow meter after completing step 3 (for example, the calculated flow or volume doesn't match the measured flow or volume), consider disconnecting the main feed hose after the flow meter (before boom valves) and run the boom for a known period of time into a calibrated drum (at least 100L), or use an accurate scale to weigh the output for a set time and calculate L/min.
Step 4: If there is a difference between actual litres per minute and rate controller litres per minute, use the following formula to fine-tune the flow meter.
Formula 1: PPU
New PPU (speed constant) | = |
Old PPU (speed constant) | x |
Rate controller speed (km/h) GPS (actual) speed (km/h) |
Using a calculator:
New PPU = Old PPU x Rate controller flow rate (L/m in) ÷ Actual (weighed) L/m in
Formula 2: Units per pulse (UPP)
New UPP (speed constant) | = |
Old UPP (speed constant) | x |
GPS (actual) speed (km/h) Rate controller speed (km/h) |
Using a calculator:
New UPP = Old UPP x Actual (weighed) L/min ÷ Rate controller flow rate (L/min))
Spraying liquids other than water (density differences)
The density of the solution being sprayed can affect the accuracy of the impeller- based flow meters, as they are factory calibrated using water. Electromagnetic flow meters will be less affected by density.
Some rate controllers allow the operator to determine a density factor. Where this feature is not available, a conversion factor can be used when spraying liquids that are heavier or lighter than water (Table 1).
To determine the density of a liquid, accurately weigh one litre of water (1000 grams). Mark the container at this point, ideally at the bottom of the meniscus.
Fill the container to the one-litre mark with spray solution from the agitated spray tank. (When testing actual tank mixes, ensure you use appropriate personal protective equipment.
Weigh this sample and record density in kilograms per litre. For example, if the spray solution is found to have a density of 1.2kg/L, using the figures in Table 1, the conversion factor would be 1.10.
Impact of density on the accuracy of the calibration
24 January 2025Impact of liquid density on the accuracy of a calibration. Another video from GRDC's Spray Application GROWNOTES™ series.
This video appears in modules 8 and 13. Craig Day: Ok, what I want to look at now is the density of spray mix and how it can affect the accuracy of your spray unit. When we’ve calibrated, we’ve used water, where one litre equals one kilo. If the mix we’re spraying is heavier than one litre per kilo, it will affect how the flow metre responds. Fortunately, we can make simple adjustments if we know the density of the mixed solution. First, I’ve measured out exactly one kilo of water and marked the litre level on a jug, creating a reference point. As you can see, this level is above the standard litre mark on the jug. Then, I prepared a 30-litre-per-hectare Easy N solution at a rate of 100 litres per hectare. Let’s weigh this mix and see what the weight tells us about the density. After weighing the Easy N mix, it has a weight of 1.08 kilos per litre. Referring to a density table, a density of 1.08 corresponds to a conversion factor of 1.04. To account for this, instead of changing the flow metre, I would go to the rate controller and enter 104 litres per hectare instead of 100. This approach avoids the need to adjust the flow metre, which could cause issues later when switching back to a solution with a lower density, such as water. By making adjustments at the rate controller, you ensure accuracy without complicating future calibrations. |
Table 1
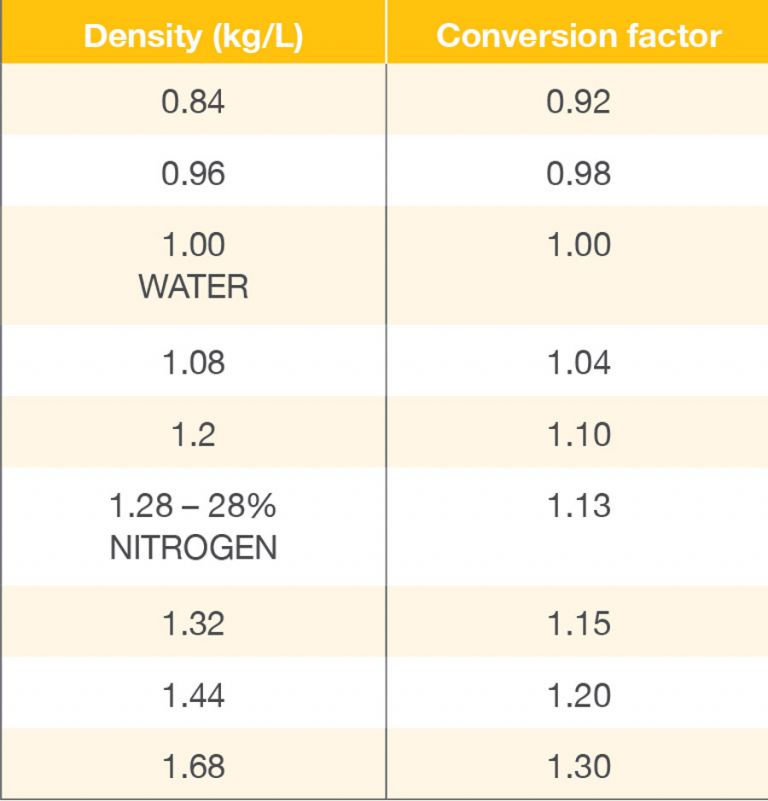
For a rate controller without density settings, use the conversion factor to manipulate the application rate. For the previous example, if the required application rate is 100hectare/ha, mix the spray solution at 100L/ha, but set the rate controller to deliver 110L/ha:
100L/ha x 1.1 conversion factor = 110L/ha
Entering 110L/ha into the controller will actually deliver 100 L/ha for the tank mix with a density of 1.2.
Applicators will notice when spraying liquids heavier than water that the pressure indicated on the pressure gauge will be higher than would normally be the case (to achieve the desired flow rate).
WARNING
Some rate controllers allow the operator to set a liquid density figure to a number higher or lower than one (where one litre of water weighs one kilogram).
If this setting is altered, the operator needs to ensure it is readjusted at the completion of the specific application.