Spray application manual
7 June 2025
Published 24 January 2025 | Last updated 20 January 2025
Nozzles are the part of the sprayer that require the most attention and have the greatest potential impact on the performance of chemicals.
When purchasing new nozzles make sure they have all come from the same batch (blister packed). Within a batch, the variation in flow rate should be less than three per cent. Flow rates between batches may vary by up to five per cent. This means that nozzles from different batches may vary in flow rate by up to eight per cent.
Ensure nozzles are calibrated under field conditions. Conduct calibrations with the nozzle operating at the average pressure (as per your spray plan).
Chemical jug weighted using accurate scales
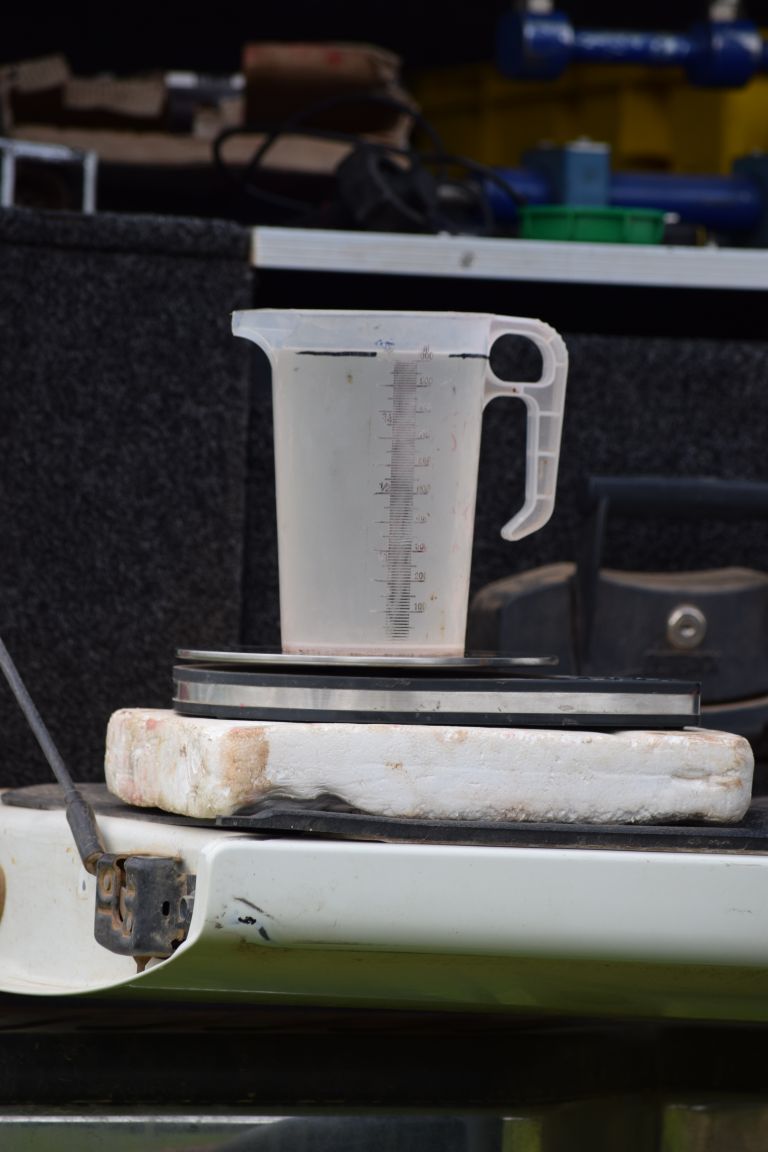
Scales for weighing nozzle output
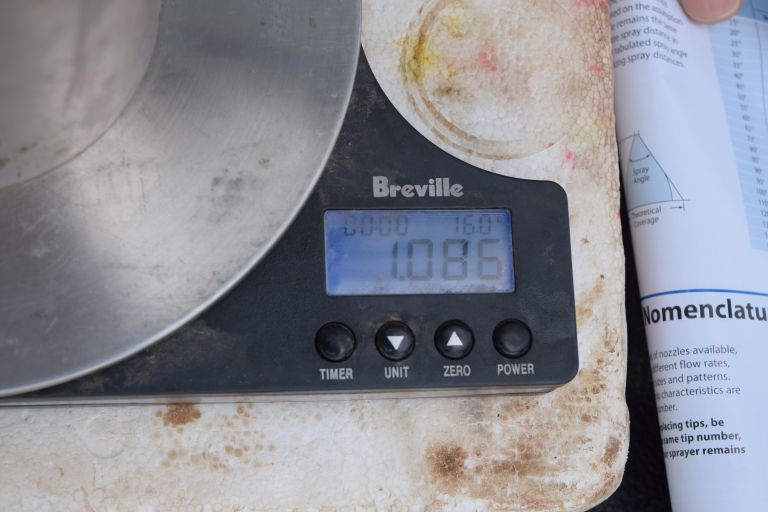
Container for catching nozzle output- weighed for accuracy
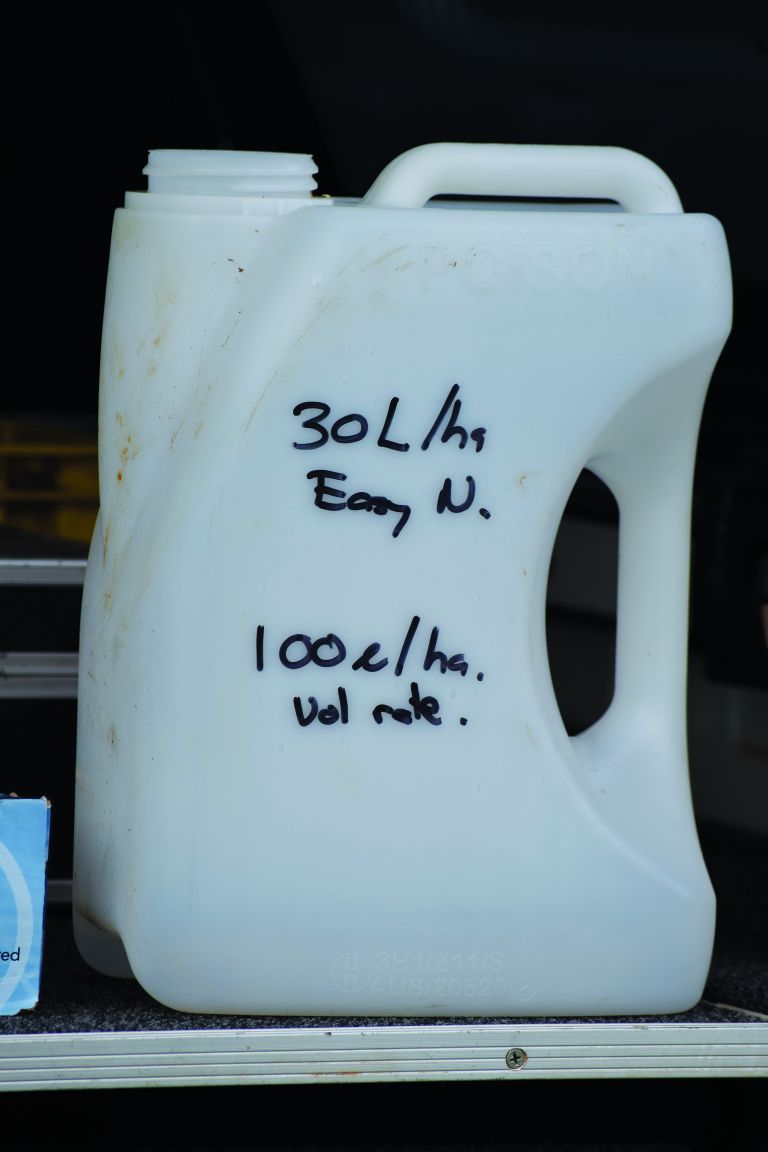
Equipment required to accurately calibrate nozzles includes:
calibrated measuring containers;
calibrated pressure gauge;
tape measure;
scales (accurate to 0.1 gram or better);
one dollar coin (reference weight = 9 grams)
nozzle chart
Steps to calibrate your nozzles
Step 1: Start clean and check nozzle patterns
Fold out the boom and operate the entire boom section. If fitted, adjust proportional return taps.
Make sure the boom has been fully decontaminated.
Operate the boom with clean water, check nozzle patterns and clean and replace nozzles where required.
Find out more
Step 2: Check pressure
Flow through pressure tester.
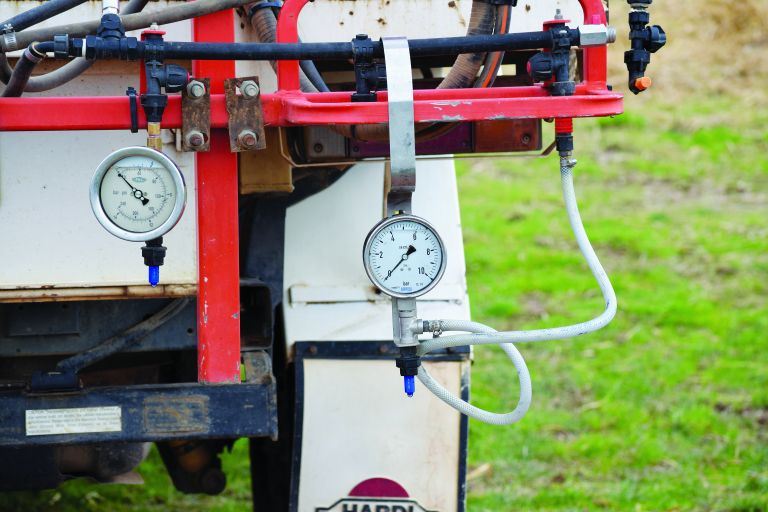
Options for measuring pressure at the nozzle
24 January 2025Options for measuring pressure at the spray nozzle. Another video from GRDC's Spray Application GROWNOTES™ series.
This video appears in modules 6 and 8. Craig Day: Okay, if we're going to look at doing pressure and flow right at the nozzle, I just want to walk you through a couple of gauge options here. These are the gauges that I use when I'm doing testing for calibration and sprayer check-out. A very simple gauge for us to make up at home incorporates a T-Jet threaded cap, a T-Jet nozzle fitting at the bottom, some gas fittings, a T-piece and preferably a rear-entry gauge. The rear-entry gauge will enable the gauge to sit vertically when doing the testing. Pressure is critical. When you're buying a gauge, if you're operating your spray system at three bar, aim for your testing gauge to have three bar at about twelve o'clock on the gauge. That'll mean the gauge will work within a very comfortable range there. If we put an inaccurate gauge on your sprayer and you go and rely on that for a test, we need to actually check the gauge we've bought. So, if you go back to your nozzle chart and look at the flow rate of the nozzle at three bar, in the case here we have an 03 nozzle that will be doing 1.2 litres per minute at three bar. So if we set this up, your new testing gauge, put it on the sprayer, set this gauge to 3 bar and actually weigh the water, we'll know how accurate your gauge is. |
Measuring pressure at nozzle and output to check flow meter
15 January 2025Measuring nozzle pressure & output to check flow metre accuracy. Another video from GRDC's Spray Application GROWNOTES™ series.
Craig Day: Righto, what we're up to now is we're going to actually check manually the pressure at the nozzle using these testing gauges. There's four sections on this sprayer, so I've actually installed four gauges. Normally what I would do is I'd go inlet and extremity of the boom section to see if there's any difference within a section. We'll set the sprayer up at three bar out here at the nozzle. Importance of that is then we can look at the rate controller and see what we're getting in a manual mode in total flow, remembering this ol' girl's got 40 nozzles on it and if we're at three bar with a lilac nozzle each one's giving us one litre. So that should be 40 litres showing up on the screen. We won't trust that, we'll actually go one step further in a while and we'll weigh that water to really see what's actually coming out. If we're not happy there, we can make some adjustments to the flow meter to give it the actual flow that's happening here at the nozzle. So the gauge is installed on the boom section, hanging there nozzle in place, with our windsock we can see the wind is going to take the mist away from us. With the gauges out on the boom we've got our three bar out of the nozzle. We come back and look at master gauge we have remarked that here, so we now know the three bar mark is here, running about 3.2 on this front master gauge which is representing three bar out there. That's going to be useful for the operator to be able to check against the spray plan against litres per minute on the screen and where the pressure gauge is sitting when the spray unit is operating. It would make good sense now to put the low pressure and the higher pressure mark on there so that when the operator's driving the spray unit the needle is between the top and the bottom mark, preferably averaging where the constant speed will be running at that three bar mark. Okay, back in the tractor, we've got our four gauges on, we know that we're operating at three bar at the nozzle, we have remarked our master gauge. With a lilac nozzle running at three bar, each nozzle will be giving us 1 litre per minute. 20m spray rig, half a metre nozzle spacings, 40 nozzles on the rig, this spray must be running fairly close to where we want it to be. 40 litres per minute showing up there on the screen. We won't quite leave it there though, we will do a measurement now in actual weight of the water on an average of nozzles and then multiply it out by 40 to give us the actual litres per minute. That will tell us what the nozzles are actually doing. If there's a discrepancy between that and the flow meter, then we can make some minor adjustments to the flow meter calibration figure. |
Check the pressure in each boom section adjacent to the inlet and ends of the section. If only using one calibrated testing gauge, set the pressure to achieve, for example, 3 bar at the nozzle outlet.
Mark the spray unit's master gauge with a permanent marker. This will ensure the same pressure is achieved when moving the test gauge from section to section.
Step 3: Check flow meter output
If pressure across a boom section is uneven check for restrictions in flow – kinked hoses, delamination of hoses and blocked filters. Make the required repairs before continuing.
When the pressure is even, set at the desired operating pressure. Record litres per minute from the rate controller display to fine-tune the flow meter (see flow meter calibration).
Without turning the spray unit off, collect water from at least four nozzles per section for one minute (check ends and middle of the section and note where the samples came from).
Step 4: Perform a rapid wear test
If checking an existing set of nozzles, install a reference nozzle. Ideally, this will be one kept aside at purchase, or, where this is not available, use a nozzle of the same brand, type and size as the one you are checking.
Keep a reference nozzle for future calibration

Check and record the output of the reference nozzle at your operating spray pressure.
Nozzle outputs are best weighed using an accurate set of scales – the increments on many jugs are not accurate.
Weight is important when calibrating air-induction or twin-fluid nozzles – the spray solution (even clean water) will include some air.
This reduces the density and makes volume-based measurements inaccurate.
Use a known test weight to check the scales for accuracy. A $1 coin weighs nine grams and is a handy reference.
Tare the jug, collect clean water from the sprayer for one minute and weigh this (one gram is equal to one millilitre).
Record the weight and calculate the flow rate of your reference nozzle.
Calculate the maximum tolerated flow rate: flow rate of the reference nozzle + 10 per cent. On a calculator this can be done by multiplying the reference nozzle flow rate (litres per minute) by 1.1.
Collect the spray from at least four nozzles per section for one minute (at the same operating pressure as the reference nozzle), weigh the outputs and compare these to the maximum tolerated flow.
If one or more of the nozzles tested per section exceeds the maximum tolerated flow, replace all nozzles.
Measuring nozzle output by weight
24 January 2025Measuring spray nozzle output by weight. Another video from GRDC's Spray Application GROWNOTES™ series.
Craig Day: Okay, to get this calibration as accurate as possible, I want to weigh the water. To do that, we need to check how accurate our scales are. A very handy reference weight is a one-dollar coin, which weighs nine grams. So, we get a one-dollar coin, pop it on the scales, and confirm it shows nine grams. Next, we weigh the water from five models, average that out, and multiply it by 40 to determine the total flow for this machine. We’ve taken our samples for half a minute, and now we’ll weigh them to see the equivalent flow. Since a kilo of water equals a litre, we can check our scales’ accuracy. After taring the measuring cylinder, we record 504 mls in half a minute. That equates to one litre plus 8 mls per minute, so everything aligns with this rig. We write down 504 for that measurement. We’ve recorded all weights for the four samples: 504, 518, 501, and 509 mls. These are over half a minute, so we double the values to calculate total flow. The total for the four nozzles is 4.064 litres. Dividing 4.064 by four gives 1.016 litres per minute per nozzle. The rate controller shows 40, so multiplying 1.016 by 40 nozzles gives 40.64. We can now adjust the flow controller’s constant to match this manual calculation. Before doing so, I’d recommend testing more nozzles, up to 20, for a more comprehensive check. Keep in mind, this calibration is based on water, but actual spraying often involves different solutions with varying densities. This can affect the flow meter. Adjustments might be needed. Additionally, consider how accurate the measuring jug is. For a straight jug test, relying solely on the jug’s markings might introduce errors. To check, I tare the jug, add a kilo of water, and compare it to the 1-litre mark. On this jug, at 960 grams, the marking is above the 1-litre mark. For better accuracy, avoid relying on such measurements alone, especially for brand-new sprayers. |
Keeping a reference nozzle
15 January 2025Keeping a reference nozzle. Another video From GRDC's Spray Application GROWNOTES™ series.
Craig Day: Alright, we're very happy with how this sprayer is performing at the moment. We’ve only checked four nozzles and verified the pressure across the unit, but keep in mind this sprayer has a new set of nozzles. Here are a few tips to remember when checking your sprayer, especially if the nozzles are older. When you install a new set of nozzles, it’s a good idea to keep one brand-new nozzle as a reference. You can use this to compare performance anywhere on the machine during pressure checks. Also, consider the placement of nozzles on the sprayer. Pay close attention to the nozzle near the inlet and those at the extremities, as these areas often experience more wear. Don’t rely on checking just a couple of nozzles in each section, as this may cause you to overlook those with greater wear. Keep your reference nozzle stored safely in a bag, mark it clearly, and put it on the shelf for future use. When needed, you can use it to compare performance with any nozzle on the sprayer. For example, place the reference nozzle in one position, test the nozzle next to it, and repeat this process across the sprayer to assess wear on the installed nozzles. |
Tip
From each set of nozzles purchased, keep one aside as a reference for calibration later on.
Step 5: Uniformity test (checking all nozzle outputs)
A uniformity check should be undertaken to check new nozzles or when the wear test shows nozzles are outside the tolerated flow range.
Uniformity tolerance for all the nozzles across the boom should be within plus or minus 5 per cent of the average flow rate for all of the nozzles.
Firstly, calculate the average flow rate per nozzle using the following formula.
Average flow rate (L/min) = total of all flow rates tested ÷ the number of nozzles tested
Then check for variation between individuals nozzles by one of the following methods.
Use an accurately calibrated jug(s) or weigh the output of each nozzle. This is the slowest, but most accurate method.
Use a tip tester – this is the fastest method for comparing output between individual nozzles. However will still require weighing of a number of samples to calculate the total flow rate through the boom if this is to be used to calibrate the controller.
Use an off-the-shelf nozzle flow meter – this is a relatively fast method, but flow meters only measure the total volume per unit of time.
Total volume may not be accurate enough to measure the outputs of air-induction or twin fluid nozzles, as the total volume may contain both liquid and air. Where air may be included in the volume, it is best to measure nozzle outputs by weight of the spray solution for a given period of time.
How to use tip testers
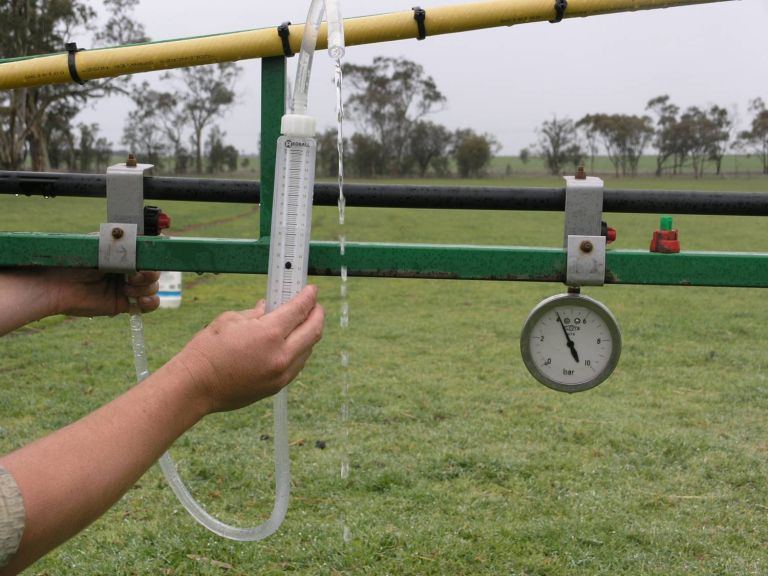
When a liquid with a density of one (water, no air included) flows through the tip tester the flow rates indicated are reasonably accurate. However, the increments of flow on some models may not be small enough
to accurately measure some of the smaller nozzles sizes (01 and 015) to plus or minus five per cent.
Typically the graduations on a tip tester increase in 40 millilitres per- minute increments. This is 10 per cent of the flow rate of a 01 orifice at 3 bar pressure (not suitable for this size), but is 5 per cent of an 02 orifice at 3 bar, which is suitable for this purpose.
Do not rely on tip testers to give an accurate reading of flow rate when testing air-induction nozzles as the density of the volume will affect the accuracy of the reading.
However, tip testers can be used for air-induction nozzles – as a measure of relativity. If a mark is placed on the tip tester for the flow rate of your reference nozzle (same air induction) at the desired operating pressure, this can be used to compare with the outputs of other nozzles.
Make sure that all nozzle outputs are within 5 per cent of the reference nozzle output, then weigh several samples from individual nozzles, calculate and record the total flow rate through the boom and the average L/min for each of the nozzles.
Step 6 Final step
Check the controller flow rate (litres per minute) against your measurements (total L/ min that was actually measured). This will give an indication of the accuracy of the flow meter and flow meter calibration.
Tips
Install a new set of nozzles before calibrating flow meters.
Check scales for accuracy – use a $1 coin (nine grams) as a reference weight. Make adjustments to scales if necessary/possible. (One litre of water is equal to 1000 grams).
Tare the jug to ensure accuracy – remember that the incremental volume marks on jugs may be inaccurate.
Discard and replace nozzles that vary by plus or minus (±) 5 per cent or more from the manufacturer’s specifications.
If installing a new set of nozzles, keep at least one nozzle as a reference for future calibration checks.