Spray application manual
7 June 2025
Published 24 January 2025 | Last updated 20 January 2025
Ideally, the shielded sprayer will be set up on a tool bar that matches the width of the seeder.
As with other sprayer set-ups, the operator needs to consider what the total volume will be that passes through the machine and associated individual components, in order to be able to select a suitable pump size and components to match this flow. The operator should also consider the agitation requirements of the tank mix.
Given the relatively low range of travel speeds for most shielded sprayers, many operators choose to set up the shielded sprayer with manual pressure control rather than attempting to use an automatic rate controller.
It is important to make certain that the hoses that supply the spray solution to each of the shields are the same diameter and the same length from the manifold, to ensure that the pressure at the nozzle is the same for each shield. If this is not practical, using proportional (adjustable three-way valves) will allow the flow to each shield to be adjusted.
Find out more
For more information on plumbing and components for the spraying system, go to Module 11: Pumps, plumbing and components
Monitoring flow under shields (for manual pressure systems)
A manual flow meter for monitoring three shields
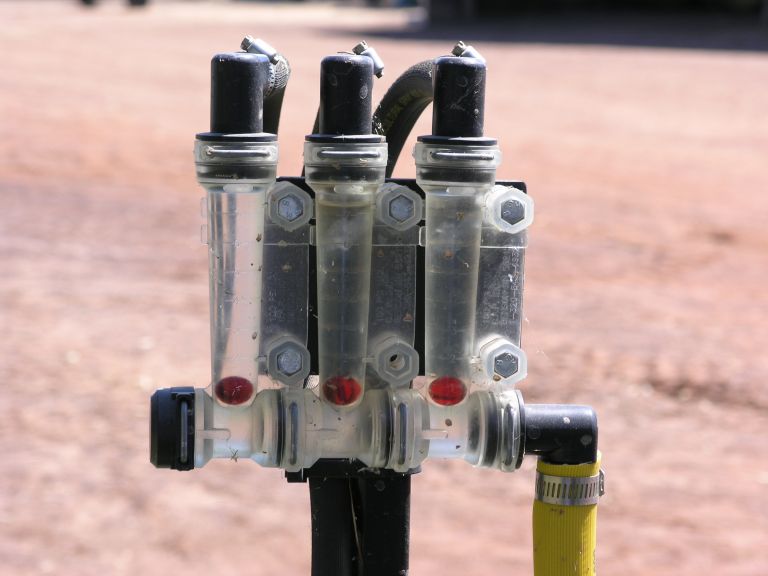
Considerations for using automatic rate controllers for a shielded sprayer
Shielded spray setups operating at low travel speeds and with a relatively small number of nozzles are likely to have low total flow rate moving through the spraying system.
Two issues to consider are the minimum flow capacity required of the flow meter, and the set-up of the regulating valve. Regardless of the pump type that is selected, the regulating valve should be used in bypass mode when low flow rates are required.
Where a rate controller is to be used, it would be ideal to treat each shield as a section, with each section allocated a sprayed width to match the shield. This way the rate entered into the controller will match the applied rate.
Where it not possible to have a single section allocated to each shield, grouping shields together as a section may be a solution, provided the section width entered into the controller is the total of each of the sprayed widths of the shields within the group, and the plumbing can deliver even pressure and flow to each shield within the group.
Determining application and mixing rates (L/sprayed ha) for shields and bands
Litres sprayed per hectare is the rate used to calculate how much chemical to put in the tank.
L/sprayed ha = litres per minute per nozzle x 600 ÷ speed (kilometres per hour) ÷ width (metres)
Sprayed ha per tank = tank size ÷ L/sprayed ha
Chemical per tank = chemical rate per ha x sprayed ha per tank
What to put in the rate controller (L/paddock ha) when using a shielded sprayer
L/paddock ha is the rate that should be entered into the automatic rate controller.
L/paddock ha takes into account how much of the paddock is actually sprayed.
When making calculations for banded or shielded applications, the L/paddock ha will always be less than the L/sprayed.
L/paddock ha = L/sprayed ha x (total width of bands or shields
÷ sprayer width per pass)
Example: A 12-metre-wide shielded sprayer set up with 11 x 0.90m shields (with 2 x 015 nozzles per shield) and 2 x 0.45 metre guess row shields (with 1 x 015 nozzle per shield). It is operated at 10km/h and a pressure of 4 bar (an 015 @ 4 bar = 0.68 L/min/ nozzle)
L/sprayed ha = 0.68L/min/nozzle x 600 ÷ 10 km/h ÷ 0.45 metres
= 90.7L/sprayed ha (mix to this rate)
L/paddock ha = 90.7L per sprayed ha x (11 x 0.9m + 2 x 0.45m) ÷ 12 metres
= 90.7L per sprayed ha x 10.8m ÷ 12m
= 81.6L per paddock ha (this rate goes into the controller)
Find out more
For more information download the GRDC Back Pocket Guide 'Nozzle selection for booms, bands and shields'.