Spray application manual
8 June 2025
Module 4: Managing spray drift risk
4.3: Drift management strategies: things that the spray operator has the ability to change
Published 24 January 2025 | Last updated 20 January 2025
Factors that the spray operator has the ability to change include the sprayer setup, the operating parameters, the product choice, the decision about when to start spraying and, most importantly, the decision when to stop spraying.
Things that can be changed by the operator to reduce the potential for off-target movement of product are often referred to as drift reduction techniques (DRTs) or drift management strategies (DMSs). Some of these techniques and strategies may be referred to on the product label.
Drift Reduction Technology an Introduction
2 March 2017An introduction to Drift Reduction Technology. Another video from GRDC's Spray Application GROWNOTES™ series.
Bill Gordon: Many people would have heard of the term DRT or drift reduction technology. From a grower's point of view these are the things that allow us to minimize the amount of product or droplets of that might get into the air while we're spraying. The things that can help reduce drift are things like boom heights, so lowering the boom height as low as practical when you're operating, but still maintaining double overlap
that's one way of cutting down how much product could get in the air.
Another thing that you could do is with your nozzle selection, so choosing nozzles with larger droplets or coarser spray qualities also reduces drift potential. There's other things as an operator you may be able to do for instance your formulation choice or the addition of adjuvants to the tank may also affect droplet size which could cut down drift and all these things when reduced drift reduce the amount of product that can move down wind or away from this sprayer.
When it comes to the APVMA - the guys that aprove products for sale and determine what goes on the label, DRT or drift reduction technologies have a very specific meaning, so on the label there will be approved DRTs which will allow growers to potentially reduce their no spray zone or that downwind buffer distance that's required for some products. The things that may be acceptable on the label in reducing a buffer may be operating at reduced wind speeds, again lower boom heights or changing droplet size. They will also recognize certain formulations as reducing drift.
So from a growers point of view it's always important to check the label and see what technologies or drift reduction technologies will be acceptable if you're looking at reducing a no spray zone.
Find out more
For more information on spraying using larger droplets see the GRDC Fact Sheet ‘Maintaining efficacy with larger droplets - 2,4-D application requirements.’
For more information on in-crop herbicide application see the GRDC Fact Sheet ‘In-crop herbicide use.’
Using coarser spray qualities
Spray quality is one of the simplest things that the spray operator can change to manage drift potential. However, increasing spray quality to reduce drift potential may require adjustment to water rates used to maintain reasonable efficacy.
Applicators should always select the coarsest spray quality that will provide appropriate levels of control.
The product label is a good place to check what the recommended spray quality is for the products you intend to apply.
In many situations where weeds are of a reasonable size, and the product being applied is well translocated, it may be possible to use coarser spray qualities without seeing a reduction in efficacy.
However, by moving to very large droplet sizes, such as an extremely coarse (XC) spray quality, there are situations where reductions in efficacy could be expected, these include:
using contact-type products;
using low application volumes;
targeting very small weeds and particularly small grass weeds with narrow upright catching surfaces;
spraying into heavy stubbles or dense crop canopies; and
spraying at higher speeds.
If spray applicators are considering using spray qualities larger than those recommended on the label, they should seek trial data to support this use. Where data is not available, then operators should initially spray small test strips, compare these with their regular nozzle set-up results and carefully evaluate the efficacy (control) obtained. It may be useful to discuss these plans with an adviser or agronomist and ask him/her to assist in evaluating the efficacy.
Find out more
For further information see the GRDC Fact Sheet ‘Practical tips to reduce spray drift.’
Spraying speed
For the majority of sprayers the most obvious impact of changes in spraying speed is on the pressure at the nozzle. On most sprayers, changing speed alters spray pressure and will result in changes in droplet size. Exceptions to this would be for those operating with manual pressure or pulse-width modulation.
Regardless of the spraying system being used, spraying speed can also influence how droplets behave close to the sprayer.
Increased spraying speeds can have impacts, including
at the nozzle, as the droplets are produced, by affecting the spray pattern and increasing small droplet escape;
at the target, by influencing how the droplets may deposit or penetrate a canopy;
altered air movement around the sprayer (aerodynamically), which affects droplet movement close to the chassis (known as the wake effect); and
adjacent to the wheels and tyres, where droplets can be displaced by increased air movement, leading to lower spray deposits.
Spraying speed
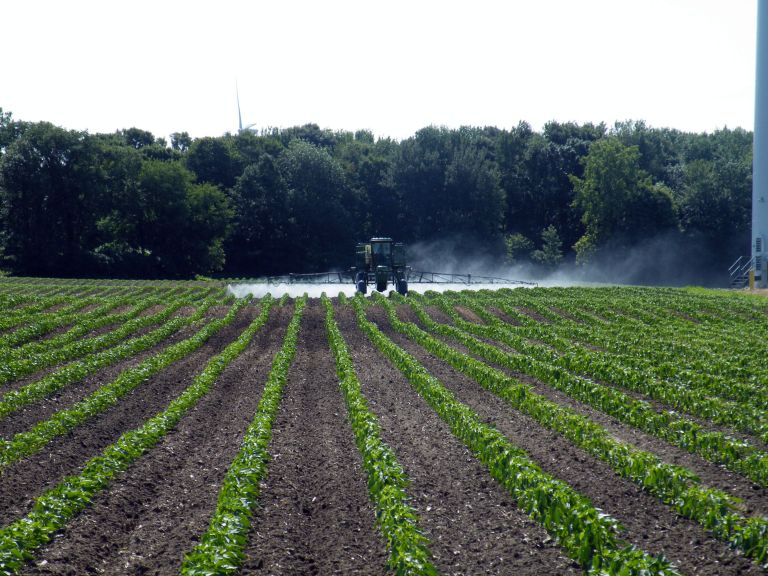
Changes in pressure at the nozzle
When using a standard single-line sprayer fitted with an automatic rate controller, increased spraying speed will increase pressure at the nozzles, which will lead to a reduction in droplet size. This is why it is important to prepare a spray plan, so you can determine the range of spraying speeds that will maintain the desired spray quality with the nozzle you have selected, and at the total application volume (litres per hectare) you intend to apply.
There are other spraying systems that can maintain the spray quality over a wider range of spraying speeds, including multi-step systems and pulse-width modulation.
Find out more
For more information go to Module 6: Pre-operational and regular checks, or Modules 16, 17 and 18 for further information on alternative spray systems.
Increased escape of small droplets from the spray pattern
Air movement past the nozzle can impact on how the spray pattern is formed and the ability of droplets to remain within the spray pattern. This impact is sometimes referred to as shear, and occurs when air movement begins to impact on the spray pattern.
When the air speed coming into contact with the spray pattern is fast enough, it can:
change the shape of the spray pattern, causing it to narrow and wrap backwards. This can impact on the overlap of the spray patterns and the evenness of the spray deposits onto the target;
cause a loss in downward velocity, which can reduce canopy penetration; and
lead to the escape of small droplets from the pattern, known as detrainment, which can increase drift potential.
Find out more
For details on how to assess spray deposits around your sprayer go to Module 21: Assessing spray deposits.
Increased wake effect
Increasing spraying speed increases the amount of air displaced by the sprayer as it moves across the ground. This can be significant directly behind the sprayer, where droplets may be transported several metres upwards into the air. Small droplets can be carried upwards by the wake, leading to increased drift potential and areas of lower deposition of droplets in the centre of the sprayer, particularly between the wheels when travelling into a headwind.
The spraying speed at which the wake effect becomes significant can change for different sprayer types. However, in general terms, at speeds above 15 to 16km/h the effect can become apparent.
Spray operators can check the droplet deposition obtained around the sprayer to evaluate the impact of spraying speed and spray quality on where the droplets actually land.
Assessing deposition in fallow & wheel tracks
15 January 2025Assessing spray deposition in fallow and wheel tracks. Another video from GRDC's Spray Application GROWNOTES™ series.
This video appears in modules 4 and 21.
Bill Gordon: We're looking at assessing spray deposition in stubble, particularly in summer time because one of the issues we have on most machines is problems in the wheel tracks and issues with dusting around the wheels, so what we've been doing is positioning water sensitive paper down in amongst the stubble, but also in the inter-row. It's important to have a reference point when you do that, so when checking across the machine we'll start out on the boom and see what the deposition should be without interference, and then we'll come back into the machine.
So what we'll do is check some deposition in the standing stubble out on the boom here. Okay we're about the midpoint of the boom out from the machine, and we placed the cards in the inter-row or between the standing stubble but also at the base and what we're looking for is comparing the deposition between the two areas, so looking at where the droplets have landed, seeing if there's enough coverage there we're going to use this as a reference point. The things we're looking for on this water sensitive paper or card is how even that is between the two. If we get to the point where these are pretty even it's a great reference point, so on this we can see fairly uniform droplets, you actually use the core spectrum here at about 80 litres of water and the two cards look very similar.
Now we can use at base programs like snap card to actually measure that deposition as a percentage coverage and we can see how close it is, cos quite often with the naked eye they'll look similar but you might not pick up the subtle differences, but these two to me look pretty even and they'll form our reference point for comparing the other cards in closer to the machine, so whatever happens here out on the boom we'll be comparing other parts of the boom particularly around the wheel tracks in the center of the machine to see if it is as good as it is here. Now if we see any issues between these, like differences between what's happening in the inter-row and the stubble line, particularly reductions in the stubble, that should be a cue to us that we need to change something either volume or pressure, maybe manipulate droplet size a little bit, so this is our reference point. If we get this right across the boom then we can go and have a look at the center and see if there's anything also we need to adjust to tweak the wheel tracks or manipulate for dust.
We're moving into the wheel track area of the machine now and it's really important focus for summer fallow spraying, not only for dust but looking at what's going on around the wheel track, so we're looking at either outside the wheel or inside the wheel and coming down to the cards, this one placed on the outside of the tyre, so we're comparing what's going on in the inter-row to the standing stubble and I can see in the standing stubble on the outside of the tyre the deposition is quite a bit lower on this card. If I come to the inside of the tyre over here, again if we look at what's going on here in the standing stubble you can see the deposition is a lot less there in the standing stubble, so what we're going to do is have a look at the setup on the machine, see where the nozzles are and see if we can make some improvements.
We come in to look at the nozzle setup on this machine, I can see it's a dual boom and that in and around the wheel itself they've actually got a larger nozzle on here to increase the flow rate, which is very common for most operators, they'll increase the flow on the wheel to try and deal with dust and wheeltrack issues, but what we've seen is that the problem is actually also on the outside of the wheel, so rather than just increasing the flow rate in one spot by in this case including a bigger nozzle, what we should do is probably spread that flow, at least look at outside of either side of the wheel to try and even up that deposition and then run those tests again to see how well we've done.
Once we've done that we can look at other areas on the machine, so while we're doing the same test, I tend to not only focus on the outside of the boom or in the wheel tracks, I'll take a measurement in the center on these particular wheels inside and outside on the other wheel and also out on the center of the boom and make the same comparisons. Remembering that our reference point is what's going on out in the boom, if we see any differences in the center around the wheels this is where we're trying to improve things to get our fallow spraying to be a little bit better.
Increased displacement around the wheels and tyres
The wheels and tyres on the spray rig tend to displace a lot of air. The faster the rotational speed of the tyres, and the more aggressive the lug pattern is, the more air will be displaced. This tends to move smaller droplets away from the wheel tracks and causes areas of lower spray deposits, particularly at the base of standing stubble. This air movement may also cause droplets to be drawn into the upward air movement behind the sprayer.
Find out more
For further information on the impact of air movement around wheels and tyres, see the GRDC Fact Sheet ‘Weed control in wheel tracks’.
Reduced penetration into stubble and crop canopies
As droplet size increases, the droplets tend to hold their direction of travel. When using coarse droplets, increasing the spraying speed tends to favour deposition on the leading edge of vertical surfaces. Very coarse and larger spray qualities applied at higher spraying speeds can also result in increased shadowing behind stubble, below crop plants and larger weeds. These effects can occur at different spraying speeds for different nozzles, with some nozzles with low-exit velocities being impacted at spraying speeds as low as 8 to 10km/h.
It is worthwhile for spray applicators to assess the impact of spray quality and spraying speed on the deposition of droplets in different situations.
Find out more
For more information on how to assess spray deposition go to Module 21: Assessing spray deposits.
Boom height
Boom height above the target is critical to ensure an even overlap of the nozzle spray patterns. For most broadacre spraying we aim to set the boom height where we can achieve a double overlap of the spray pattern from each nozzle. Double overlap is achieved when the outer edge of the spray patterns arrive at the target area in alignment with the adjacent nozzle.
The weeds to be sprayed in Figure 2 are 0.02 metres (2cm) high but the false target, the crop, is 0.3 metres high. If we are using 110° nozzles at 0.5-metre nozzle spacing, the nozzles need to be no lower than 0.8 metres above the ground (0.5 metres above false target).
Achieving double overlap
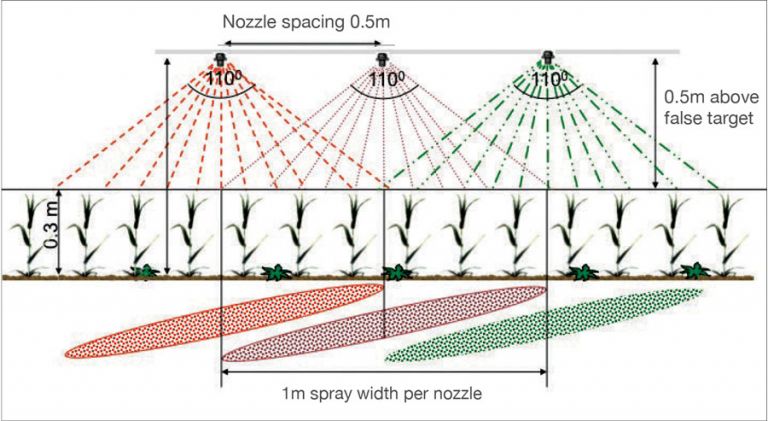
Wider fan angles can allow for lower boom heights, but the trade-off will be an increase in drift-prone droplets compared to narrower-angled fans (for example, when comparing a 110° nozzle with an 80° nozzle).
While nozzles with narrower fan angles tend to produce less drift-prone droplets than the same type with a wider fan angle, the boom will need to be adjusted to ensure sufficient overlap occurs.
Increasing the boom height above what is required to achieve the overlap will increase the amount of chemical that remains in the air because the smaller drift-prone droplets lose their downward velocity very quickly. The amount of increase in drift potential is related to the size of the droplets, their initial velocity and the rate at which they slow down.
Research has shown that when using the same nozzle type at the same pressure, increasing boom height from 50 to 70cm above the target can increase the amount of drift produced by as much as four times.
An increase in boom height from 50 to 100cm can result in a 10-fold increase in the amount of drift produced for some nozzles.
Find out more
For more information about height control systems go to Module 14: Boom stability and height control.
Product choice
The choice of active ingredient and formulation can influence the droplet sizes produced by a nozzle, as well as the level of damage that may occur, should spray drift leave the field.
In all situations it should be the responsibility of the applicator to ensure spray drift remains within the treated area.
To provide additional environmental safety, several product labels contain downwind buffer zone requirements, other restraints and directions such as wind speed, spray quality and/or water rates to be used.
Buffer zone information is typically specific to application method. For example the distances may vary from aerial to ground based application. Buffer zones distances may be required for, and differ between, downwind hazards such as bystander areas, natural aquatic areas, pollinator areas, vegetation areas, and/or livestock areas.
Buffer zone information and spray drift label directions are specific to individual products and may vary between different activate ingredients and formulation type.
Where downwind buffers or no-spray zones are present on the product label, they can provide a useful basis for identifying which products may present a lower risk than others.
In certain situations it may be recommended to switch to a less damaging active ingredient if there is a known highly sensitive hazard in downwind proximity.
Rate of product
Robust product rates are important for efficacy and minimising resistance development. However, the rate of product used may also affect the level of damage that could occur if the product moves away from the target area.
The rate of product applied per hectare can influence:
the total amount of the active ingredient available to move off-target;
the concentration of the active ingredient within each droplet; and
the concentration of adjuvants and additives within the spray solution, which can impact on droplet size.
Higher rates of product increase the total amount of active ingredient released into the environment and this can result in the need for increased downwind buffer distances.
Where more active ingredient is released, a greater distance downwind is required to allow for sufficient dilution to occur to reduce the concentration at which the airborne droplets will deposit onto the surface.
Without increasing the total application volume (water rates), higher rates of product mean that each droplet will be more concentrated, this can lead to increased levels of damage if those concentrated droplets deposit onto a sensitive area or crop.
Increasing the concentration of the active ingredients also increases the concentration of other additives in the spray solution. Where products have a high surfactant loading, increasing the rate of product can result in an increase in the number of driftprone droplets that are produced. In other situations, where the product is formulated as an emulsion, increasing the rate of active may have little effect on droplet size, or may actually reduce the number of drift-prone droplets.
It is important to evaluate the impact that changes in rate or additions to the tank mix may have on droplet size. Assess claims made by manufacturers carefully and access tools that may assist in decision-making.
Adjuvants and tank-mix partners
The addition of some adjuvants and other products to the tank mix can change the spray quality in ways the spray operator may not have anticipated.
The addition of wetters and spreaders (commonly called surfactants) that reduce surface tension will generally result in smaller droplets being produced, whereas the addition of oils and products that increase viscosity will generally increase droplet size.
Note: Many common ‘spraying oils’ used in Australia are a combination of an oil plus a high rate of spreading surfactant. This can often mean that the benefit of the oil is negated by the surfactant. From some pesticides, the addition of the ‘spaying oil’ may be neutral, or even detrimental, to spray drift.
To understand how the addition of an adjuvant or other product(s) to the tank mix will impact on droplet size it is important to understand the terminology used to describe nozzle outputs and use this to evaluate the information supplied by product manufacturers very carefully.
Where a manufacturer does not provide detailed information to support claims about changes to droplet size or drift reduction, the spray operator should be sceptical about such claims. All claims should be supported by statements on the Australian Pesticides and Veterinary Medicines Authority (APVMA)-approved label, which tells the spray operator that there is some scientific rigour behind the statements.
Find out more
More information about the properties of spray adjuvants can be found in the GRDC booklet ‘Adjuvants: Oils surfactants and other additives for farm chemicals’.
Adjuvant type
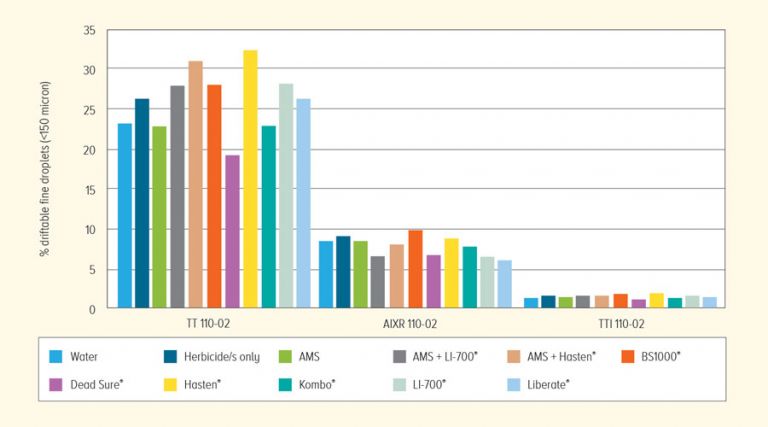
A GRDC study (Graph 3) conducted by the Centre for Pesticide Application and Safety (CPAS) at its wind tunnel facility at University of Queensland, Gatton, evaluated the droplet spectrum produced by a range of adjuvant and fallow herbicide combinations across three different nozzle types (all 110-02 (yellow) nozzle size, operating at 4 bar pressure):
Turbo TeeJet® (TT) - fine end of medium
Air Induction Extended Range TeeJet® (AIXR) - coarse end of medium
Turbo TeeJet® Induction (TTI) - ultra coarse.
As can be seen from the graph above, the selection of nozzle type has the greatest impact on the percentage of driftable fine droplets produced.
The addition of ammonium sulphate (AMS and Kombo® type products) typically had minimal effect on droplet size, where it was not mixed with an additional surfactant.
Adjuvants that contain significant levels of surfactant (BS1000®, LI-700®, Liberate®, Hasten®) all increased the volume of spray present as droplets <150 micron with the finest of the nozzles tested (Turbo Teejet®). As the nozzles became coarser, this effect diminished.
The guar gum-based adjuvant Dead Sure® consistently provided a reduction in volume of droplets <150 micron across all the various nozzles and herbicides tested.
A wide range of herbicide combinations were also tested in this study (data for all herbicides and combinations grouped in the graph). Generally, solvent-based herbicides (such as emulsifiable concentrates) or herbicides with in-built surfactant tended to slightly increase the volume of droplets <150 micron, however, the effect of herbicides was typically third in order of importance behind selection of nozzle type and adjuvant, respectively.
Sprayer type and design features
There are several spraying systems available that have the potential to reduce the amount of spray drift that may be produced, provided they are operated correctly and in appropriate conditions.
In general terms, systems that increase productivity during favourable conditions for spraying can help to reduce the risk of product moving away from the target area, by not requiring applications to be made under unfavourbale conditions. Increasing boom width, providing height is maintained, can lead to an increase in the number of hectares sprayed per hour. This can be a positive outcome when weather conditions are good, but can have negative consequences when conditions are wrong, simply by leaving more chemical in the air for each hour of spraying.
Spraying systems that have been shown to be able to reduce the potential for spray drift achieve this in different ways, some techniques include the following.
Shielded or shrouded sprayers
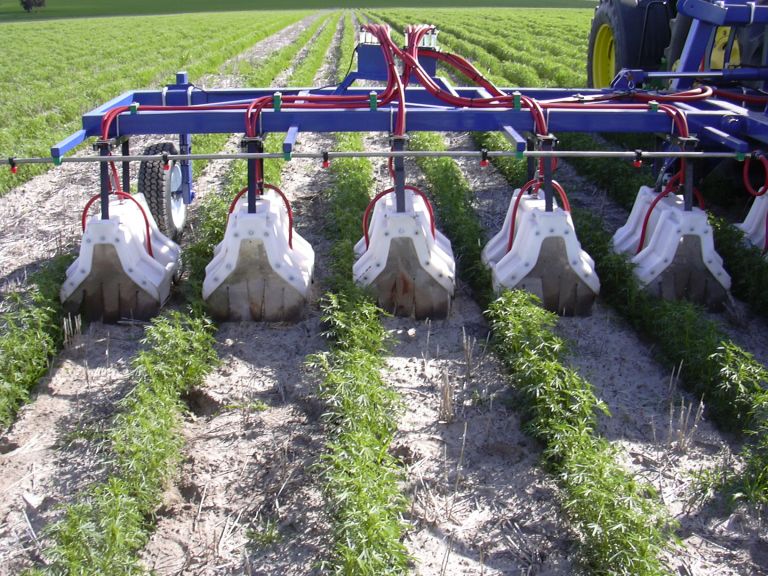
Shielded and shrouded sprayers can reduce spray drift by preventing droplets from becoming airborne. Many designs can reduce spray drift by more than 99 per cent, provided they are operated at appropriate speeds and the shield is maintained close to the ground.
Optical spot sprayers

Integrating optical spot sprayers under shields
There are currently shielded sprayers that have integrated a WeedSeeker® system under the shields, for spot spraying weeds in the inter-row.
The choice of optical spot sprayer system is limited by the required height of the sensor above the target. The WeedSeeker® sensors can operate at about 0.65 metres above the target, and have been fitted to commercially available shielded sprayers.
Air-assisted sprayers
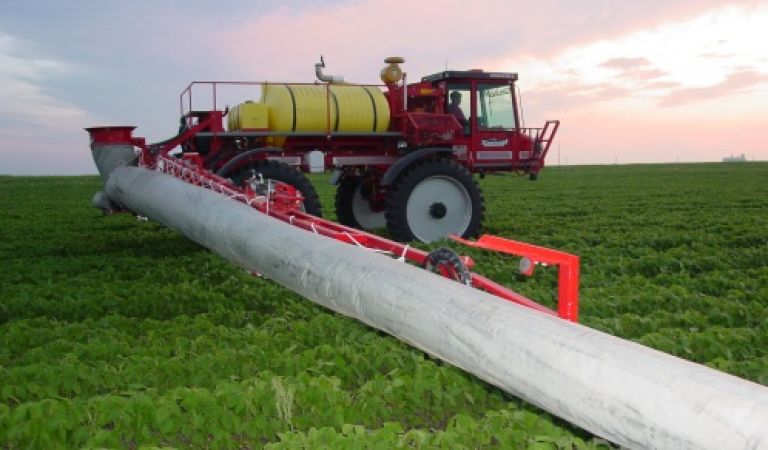
Air-assisted sprayers use conventional hydraulic nozzles and an airstream to assist the transport of droplets to the target. Well-designed and operated air-assisted sprayers can help to constrain droplets within the airstream, reducing the potential for smaller droplets to become airborne.
In many European countries air-assisted sprayers are legally able to operate closer to sensitive areas than conventional booms. However, if they are not correctly operated, such as using finer droplets and high air speeds when there is little or no crop canopy to catch the droplets, they can increase the amount of drift produced compared to a conventional boom.
Vegetative barriers
Casuarina species
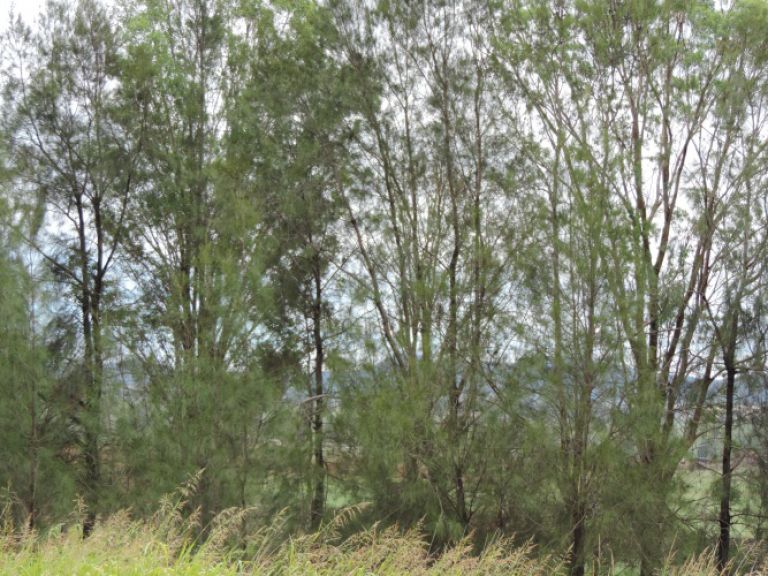
Vegetative barriers are areas of vegetation deliberately planted by the landholder to intercept and filter airborne droplets. Generally, one or two rows of an appropriate species can intercept up to 70 per cent of airborne droplets if they have been chosen to allow for air movement through the foliage and have leaves that are effective at catching small droplets.
The ideal vegetative barrier would be made up of drought-tolerant species with long, thin, cylindrical leaves, such as Casuarina species. The vegetative barrier height should be at least 1.5 times greater than the release height of the spray, and it should have a porosity (openness) of about 50 per cent.
Porosity, can be judged by looking at the amount of light passing through the canopy. A porosity of 50 per cent will appear to have about 50 per cent light and 50 per cent dark (foliage) when viewed from a position parallel to the plant line.
The vegetative barrier only needs to be about 15 to 20 metres wide, with an area of about 10 metres free of vegetation on either side, to be highly effective.
DRT - vegetative barriers
2 March 2017Drift Reduction Technology - vegetative barriers. Another video from GRDC's Spray Application GROWNOTES™ series.
Bill Gordon: So I'm looking at a group of trees behind me that have been deliberately planted to act as a vegetative barrier. Now the idea of the trees is to act as a filter to take out droplets from the air. The ideal structure for this is to have it about fifty percent light and dark when you look at it so it has porosity or openness. If it's too open it'll allow too much spray through; if it's too closed the spray will actually just go up and over like a solid wall. The ideal species to put in a vegetative barrier is something with long, thin, needle-like leaves, like the casuarina in the background.
If we're looking at ideal porosity, the lower half of that tree is actually quite thick—probably looking at about seventy or eighty percent—but the upper half is probably about the right sort of openness. We could probably manage that a little bit better, take some of the vegetation out, but one of the key things is that as we look at these buffers, we also want to make sure that there's no big gaps. So if I just follow up this way a little bit, you'll see that as I go up the hill there's some pretty big open areas here. Now if we're going to plant these and try and maintain them and maintain their effectiveness, we need to make sure that we don't have gaps like that because they'll act as funnels.
DRT - vegetative barriers establishment
2 March 2017Establishment of vegetative barriers to reduce spray drift. Another video from GRDC's Spray Application GROWNOTES™ series.
Bill Gordon: Just walking alongside a vegetative barrier that's being established by this grower, and as you can see they've selected a casuarina type species, very effective at capturing small droplets, it's not quite at a stage where it's going to be a completely effective as a vegetated barrier, but these guys will still catch droplets even at this size, so we need to be very careful in establishing them and spraying next to them to avoid damaging it. Once they are established we can use things like knockdown herbicides alongside them, but just try to avoid using residual herbicides or things that might get into the roots, otherwise we're likely to damage them.
Drift Reduction Technology - Casuarina
2 March 2017Drift Reduction Technology - Casuarinas. Another video from GRDC's Spray Applications GROWNOTES™ series.
Bill Gordon: Behind me is a single row of casuarinas. They're quite tall, and as you look behind me you'll see there is approximately fifty percent light and dark as you look through them. That's the best indicator of porosity or the amount of airflow you can get through the trees. The thicker that canopy is, the taller they need to be to compensate. So with this sort of porosity or amount of light and dark, you need to be about one and a half times the release height of the spray.
One of the great things about casuarinas is that, because they're drought-adapted, they tend to have a thick, waxy cuticle, which helps resist the uptake of chemicals. This means if you plant a species like this in a vegetative barrier, they're more likely to survive and keep doing the job they're designed for, which is to filter the droplets out of the air.
DRT - barrier structure
17 December 2024Drift Reduction Technology - barrier structure. Another video from GRDC's Spray Application GROWNOTES™ series.
Bill Gordon: I want to talk briefly about the structure of a vegetative barrier. To be effective, they don't have to be particularly wide. You only need a single or two rows of trees, or a set to cover an area about 10 metres, and ideally have a gap either side of up to 10 metres that allows for a bit of vegetation management and things like that. When we look at the trees themselves, to be effective they need to be at least twice the height of the spray release, so generally 2 to 3 metres high, and they start becoming quite effective for ground application; they may need to be a little bit higher for aerial.
The other thing we would like to see is that the skirt comes down to the ground. If you're planting predominantly species that have a high skirt, maybe add some small shrubs along the base. For something like the casuarina species here, you see the skirt goes right down to the ground. It's got great thin needle-like leaves that help filter droplets out of the air and it's often an appropriate height. When I look at this, there are parts of it that are a touch thick; in other words, probably not porous enough, as the droplets will travel around them. So a little bit of maintenance on this tree, like trimming back a few branches, would help keep it very effective.
A vegetative barrier like this, up to 10 metres wide with a couple of rows of trees and a 10-metre gap either side, can be very effective at filtering small droplets out of the air. That 40 metres is equivalent to reducing up to 300 metres downwind when we're spraying beside it, so they're very effective, particularly on the predominantly downwind side of the paddocks, at filtering out droplets and helping protect sensitive areas on the downwind side.