Spray application manual
7 June 2025
Published 24 January 2025 | Last updated 20 January 2025
The main reason to consider boom re-circulation is the ability to prime the boom line with the tank mix before having to turn the nozzles on. This eliminates the need to flush the tank mix through the boom line in the paddock.
Boom re-circulation is also very useful to reduce the likelihood of products settling out in the boom line when the nozzles or boom sections are turned off as the spray solution in the boom lines can be returned back to the tank.
Benefits of boom recirculation
7 January 2025The benefits of boom recirculation. Another video from GRDC's Spray Application GROWNOTES™ series.
Bill Gordon: So this particular system here, where we've got the two nozzles fitted, is turned on and off by an air valve connected by this tube to an air solenoid back at the sprayer. This allows us to get almost an instant on and off at the nozzle, and it's very good for switching between the two.
Once you've fitted control at the nozzle, whether it's with an air valve or a solenoid, turning off here allows you to have flow in the line or a return line back to the tank. That can mean the boom is fully primed or charged when we go into the paddock, so you're not waiting for that to happen. It can also, when you have the nozzles off, reduce settling in the line, which helps minimise blockages. So that flexibility of having a valve like that or an electric solenoid to control this particular system can be very useful.
Manual boom re-circulation
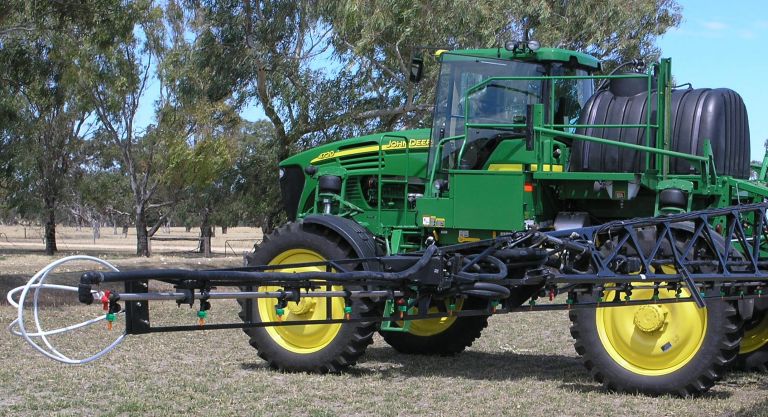
A possible drawback to having a boom re-circulation system is the possibility that diluted product may be returned back to the main spray tank, which makes most re-circulation systems incompatible with direct-injection systems.
Setting up boom re-circulation
The general idea for a re-circulation system is to have a return line from the end of each of the boom sections that takes liquid back to the top of the tank. This will keep the tank mix products circulating when the nozzles are turned off.
Normally this can be achieved by having a common return line that runs along the boom to the top of the tank, where each of the boom section return lines are plumbed into using T-pieces.
Using re-circulation requires that the nozzles are able to be shut off to prevent flow coming out of the nozzles while the re-circulation is engaged.
There are a range of air shut-off nozzle bodies and electric shut-off nozzle bodies that can turn off the nozzles while allowing liquid to flow through the boom section.
Electric nozzle shut-off valve
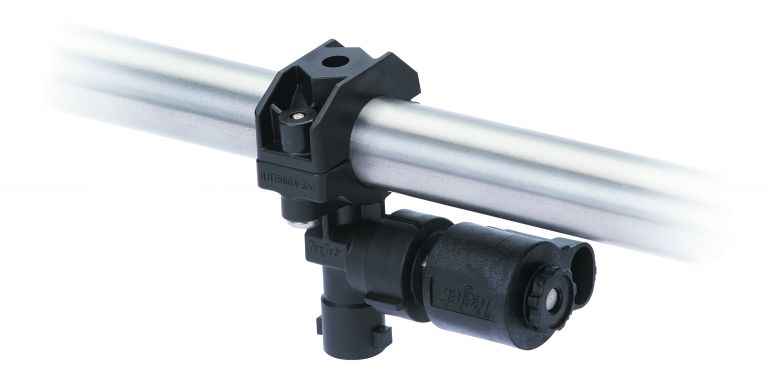
An alternative system to allow flow to return to the tank while the nozzles are shut off is to fit non-drip check valves that only open at higher pressures (e.g. rated to open at a minimum pressure of 2.0 bar); this way liquid can be re-circulated at lower pressures (1.0 to 1.5 bar) without the nozzles opening.
To be able to control the ‘engagement’ or ‘disengagement’ of the re-circulation system requires that a valve be installed between the end of each boom section and where the flow from the section is fed into a common return line to the tank when the valve is opened.
It is also useful to have an additional valve at the end of the common return line, just before the return line enters the tank. This allows the common return line to be isolated if repairs or decontamination are required. As with other plumbing on the sprayer, it is important to use fly-nut-and-tail fittings to make access, servicing and maintenance easier.
Boom re-circulation

Re-circulation system
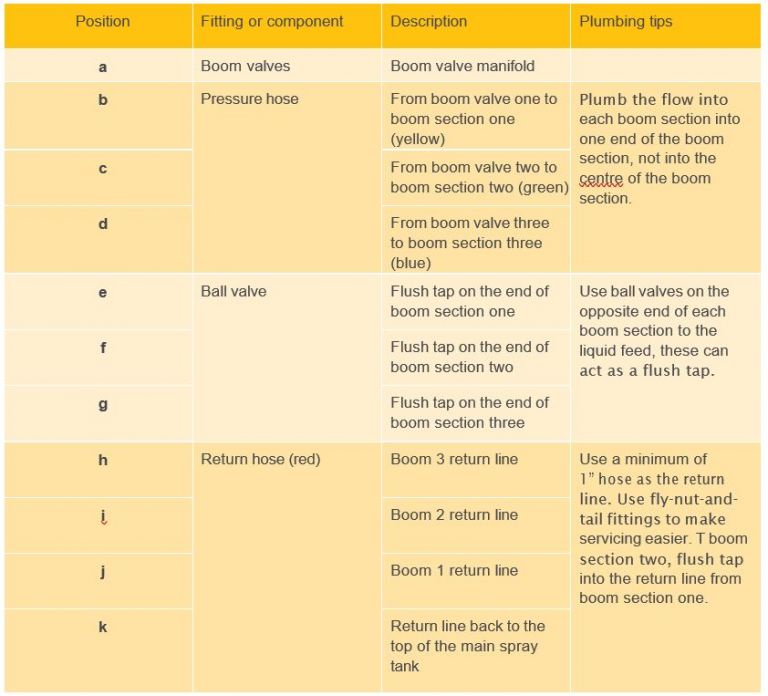
Options for setting up a re-circulation system
Establish a common return line that runs along the booms and back to the top of the tank.
Manual return line into the top of the tank
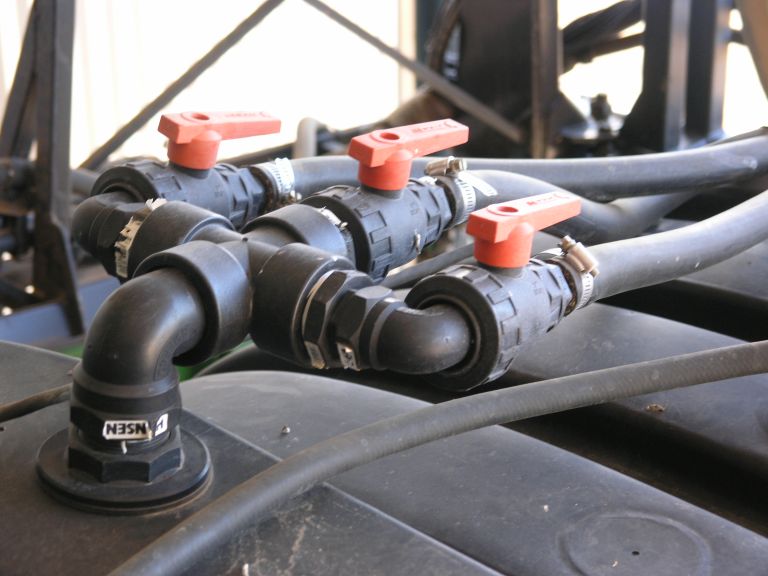
End of boom manual boom re-circulation
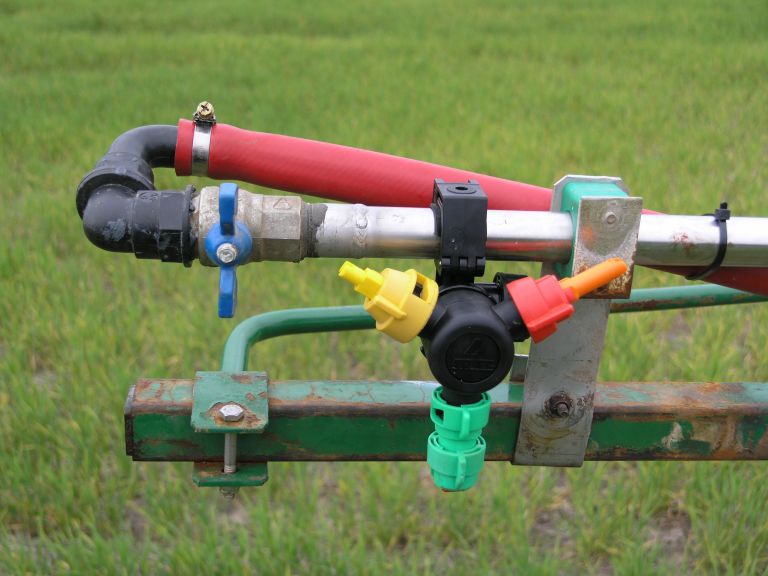
Along the boom manual boom re-circulation
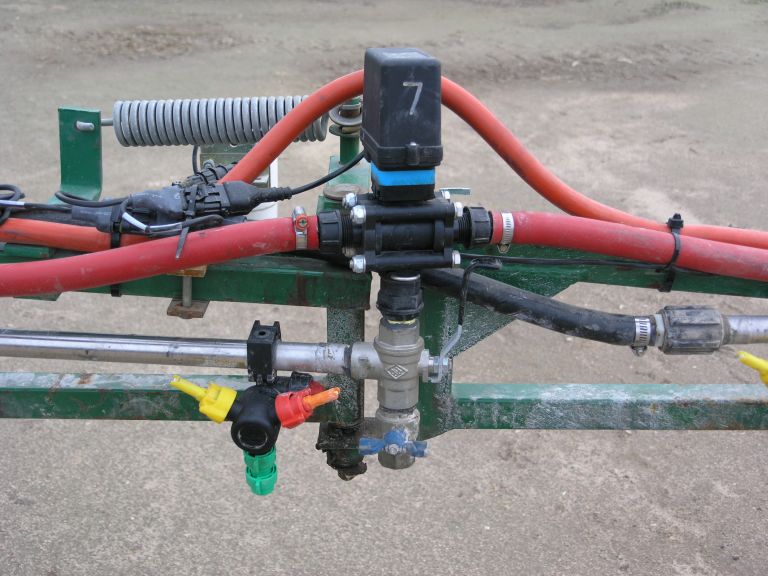
Attach a return line for each section into the common return line. This should run from the manual ball valve to a T-piece installed into the common return line.
Between the common return line and the top of the tank, install another manual ball valve close to the tank.
The basic electric option
Set up the plumbing as in ‘basic option’, with manual ball valves at the end of each boom section.
Replace the manual ball valve at the top of the tank with an electric ball valve (at the end of the return line).
The best option
Set up all the plumbing as in ‘basic electric option’, with electric ball valves at the end of each boom section, and an electric ball valve on the return line at the top of the tank.
Along the boom electric boom re-circulation
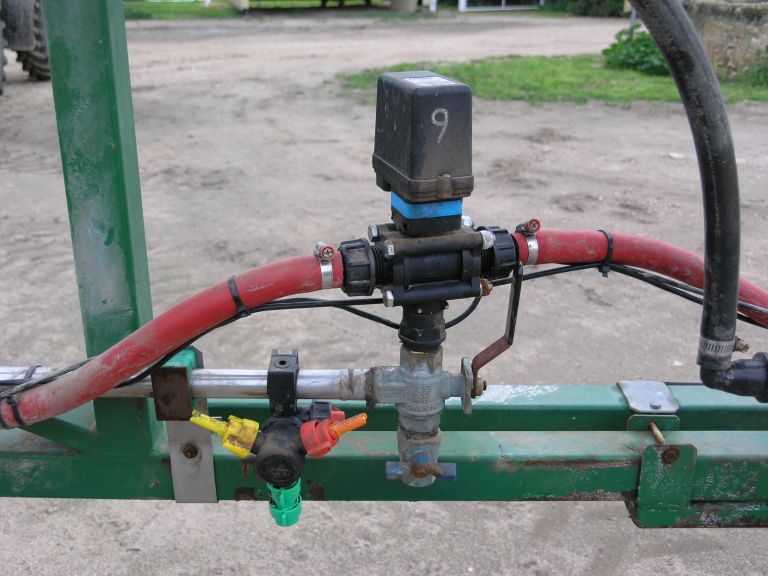
End of boom electric boom re-circulation

Re-circulation ball valve positions for different purposes
Ball valve positions when priming the boom
Turn the ball valves located at the end of the boom sections and at the top of the tank to the ‘open’ position, then, with the pump operating, turn each of the boom sections switches in the controller to the ‘on’ position.
If the sprayer has non-drip check valves on the nozzle bodies to prevent flow (e.g. rated to open at 2.0 bar), ensure there is only 1.0 to 1.5 bar pressure in the spray line to ensure the nozzles do not start to spray.
Ball valve positions when spraying
Just prior to spraying after, the boom is primed, unfolded and turn the boom sections to switch off position at the controller (to stop the re-circulation).
Turn the ball valves at the end of the boom sections to the ‘closed’ position. This will cause the spray solution to come out of the nozzles once the switches to the boom sections on the controller are turned on again.
Ball valve positions when flushing the system
If the tank is empty at the end of a spray job, clean water from the flush tank may be used to flush the re-circulation system; however, this will send some diluted product back to the tank.
Turn the re-circulation valves at the top of the tank, and at the end of each boom section to the ‘open’ position. (Check the system pressure if using non-drip check valves to stop flow from the nozzles.)
Turn the boom section switches in the controller ‘on’ and flow will now return to the tank.
Disconnecting return lines for decontamination
After adding an appropriate decontamination agent to the tank, use the re-circulation system while agitating the tank. Allow the cleaning products to stay in the tank and re-circulation system for an appropriate amount of time, then drain the tank and rinse with clean water.
After rinsing and draining the tank, avoid any product remaining in the re-circulation system returning to the tank. Disconnect each of the boom section return lines from the valves at the end of each boom sections to allow for an open flow (this may be done by removing fly-nut-and-tail). Engage each boom section switch on the controller, one at a time, to maximise flow through each section of the boom.
Once the boom sections have been flushed with clean water, reconnect the return lines to the valves at the end of the boom sections and disconnect the common return line from the ball valve at the top of the tank, then flush clean water through the common return line.
The decontamination agents and number of flushes should follow the procedures outlined in Module 7, ‘Mixing and decontamination requirements’.
Find out more
For more information go to: Module 7: Mixing and decontamination requirements.