Spray application manual
7 June 2025
Published 24 January 2025 | Last updated 20 January 2025
The purpose of regulating valves is to ensure the required volume of liquid is delivered to the boom or boom sections in response to changes in spraying speed or the operation of section control. To do this, the liquid flow from the pump must either be restricted (throttle mode for centrifugal pumps) or diverted back to the top of the main tank (bypass mode for diaphragm pumps). Check regulating valve motor speed. Faster motor speed is required for automatic rate controllers while slower motor speed may be suitable for electric manual systems.
TeeJet regulating valve
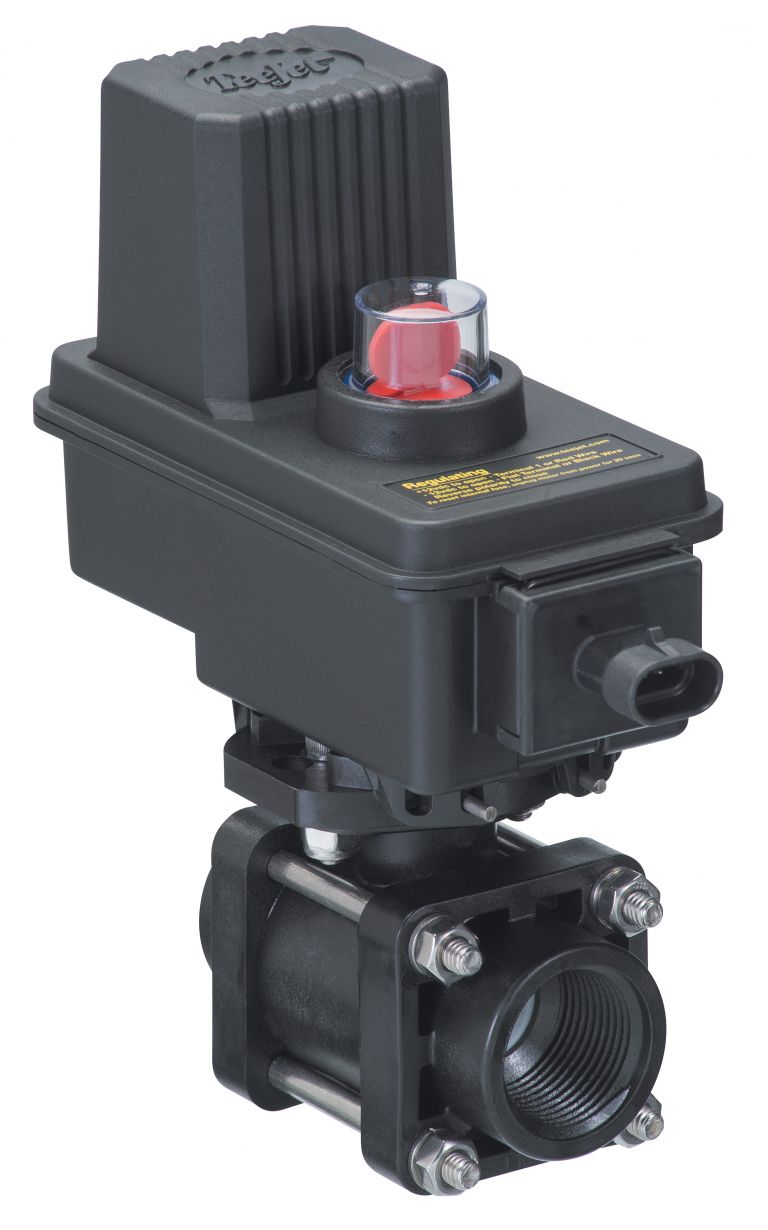
Operators should be aware that each sprayer manufacturer may use several different types of regulating valves on their particular brand of sprayer, which they may change between models or over time.
Common types of regulating valves include ball valves, plunger valves and butterfly valves.
The shape of the orifice in the regulating valve can be important to how it functions. The standard ball (R-type valve) provides the least sensitive regulation, whereas other variations on the orifice shape allow for more sensitive regulation of flow.
Ball regulating valves
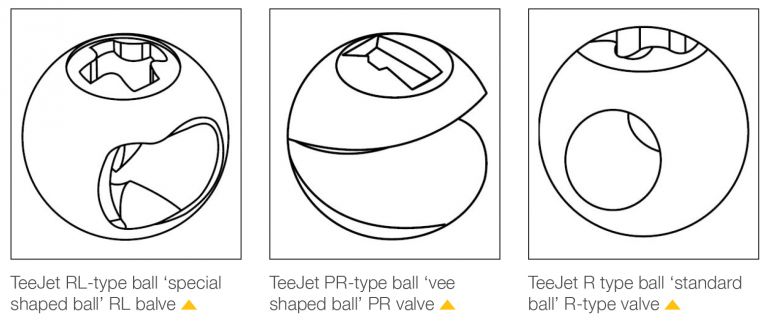
ARAG® stainless shaped ball
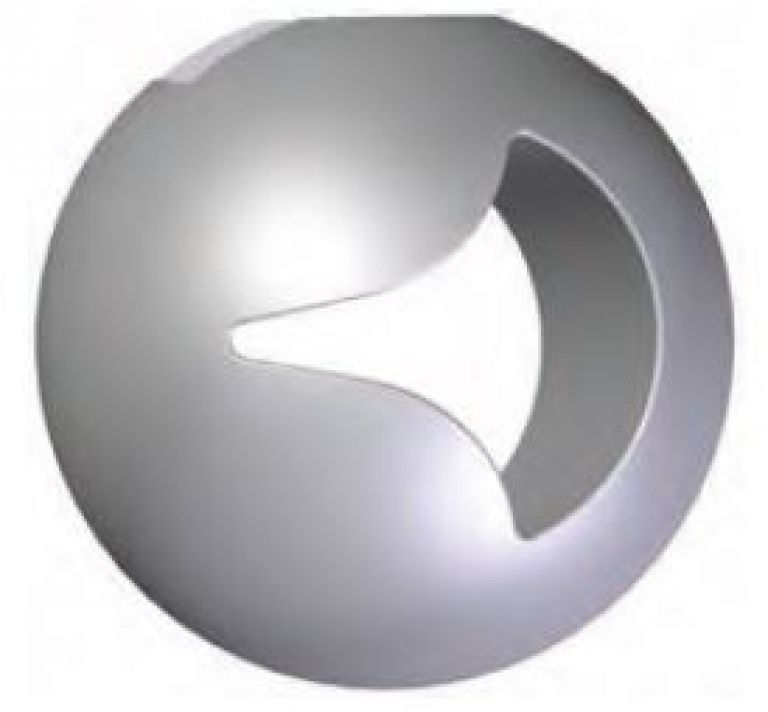
ARAG® proportional regulating valve
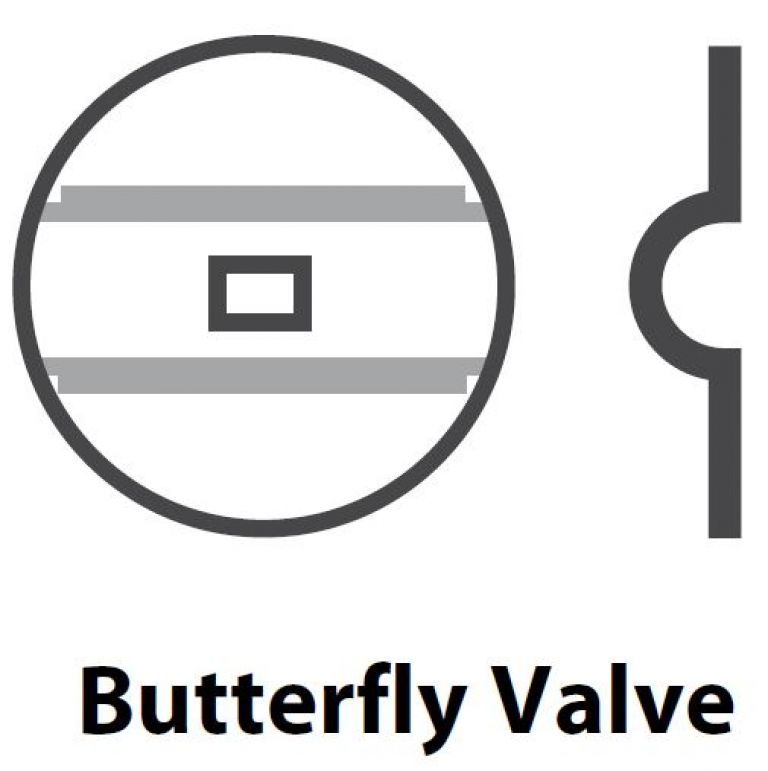
ARAG proportional regulating valve
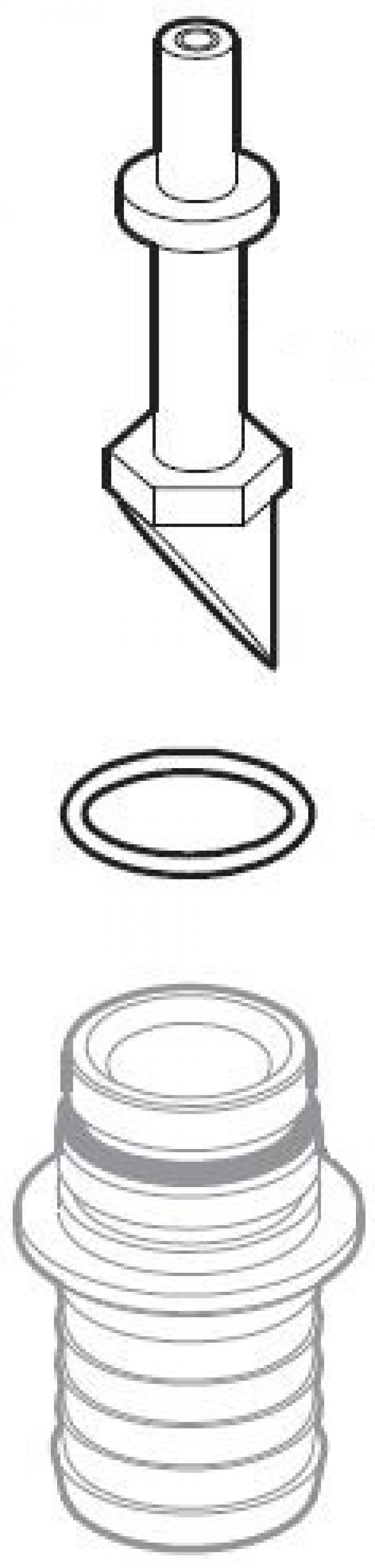
Installing regulating valves for different pumps and uses
For diaphragm pumps, install regulating valves in bypass mode. The regulating valve should be plumbed to the side of the pressure line, before the flow meter, with the bypass flow going back to the top of the tank (see figures 5 and 6, for examples of how regulating valves may be plumbed for diaphragm pumps).
For centrifugal pumps, install regulating valves in throttle mode. The regulating valve should be plumbed into the pressure line that is going to the boom valves (see figures 7 and 8, for examples of how centrifugal pumps and valves may be plumbed).
The only exception to using throttle mode on a centrifugal pump may be when trying to control low liquid flow rates (e.g. liquid systems on seeders / planters). For low flow rates with a centrifugal pump, it is a good idea to install the regulating valve in bypass mode, with the additional flow going back to the top of the tank.
Most self-propelled sprayers do not have a regulating valve in the liquid system, they regulate the liquid flow to the boom by adjusting the hydraulic oil flow to the hydraulic motor on the spray pump.
Find out more
For more information on setting regulating valves, go to Module 6: Pre- operational and regular checks.
Tips
For liquid systems that use regulating valves, always check the pressure rating of the valve and that the regulating mechanism suits your application.
It is very important to set the position of the ‘butterfly’ or ‘ball’ within the regulating valve correctly to get the best out of the sprayer. Performing a pre-field check using the simulated speed function is very important for checking that the valve settings are appropriate.
Avoid using one regulating valve for both filling operations and controlling the sprayer output. A good solution is to two separate systems: one system for spraying and agitation, and another independent system for chemical transfer. Switching between the two systems can be achieved by using continuous flow three-way ball valves to avoid dead-heading either system.